Quality in construction is crucial and is given the most importance in accessing the value of the property built. But maintaining and managing quality is also a sophisticated process. When one talks about quality control a central quality control seems to be an effective way.
But in the central quality control system, the most important bit of the puzzle is the hierarchal system of data transfer and dual approval requirement in order to ensure quality. But how is it done? What are the roles and responsibilities? Let’s discuss this in detail and get a better understanding of it.
Levels of Quality Control Inspectors:
The primary structure of any system consists of a system of hierarchy of how data flows within the system and who is responsible for which of the actions. Similarly, in central quality control system there are four levels of inspectors appointed for quality assurance and quality control. Listed below are the levels:
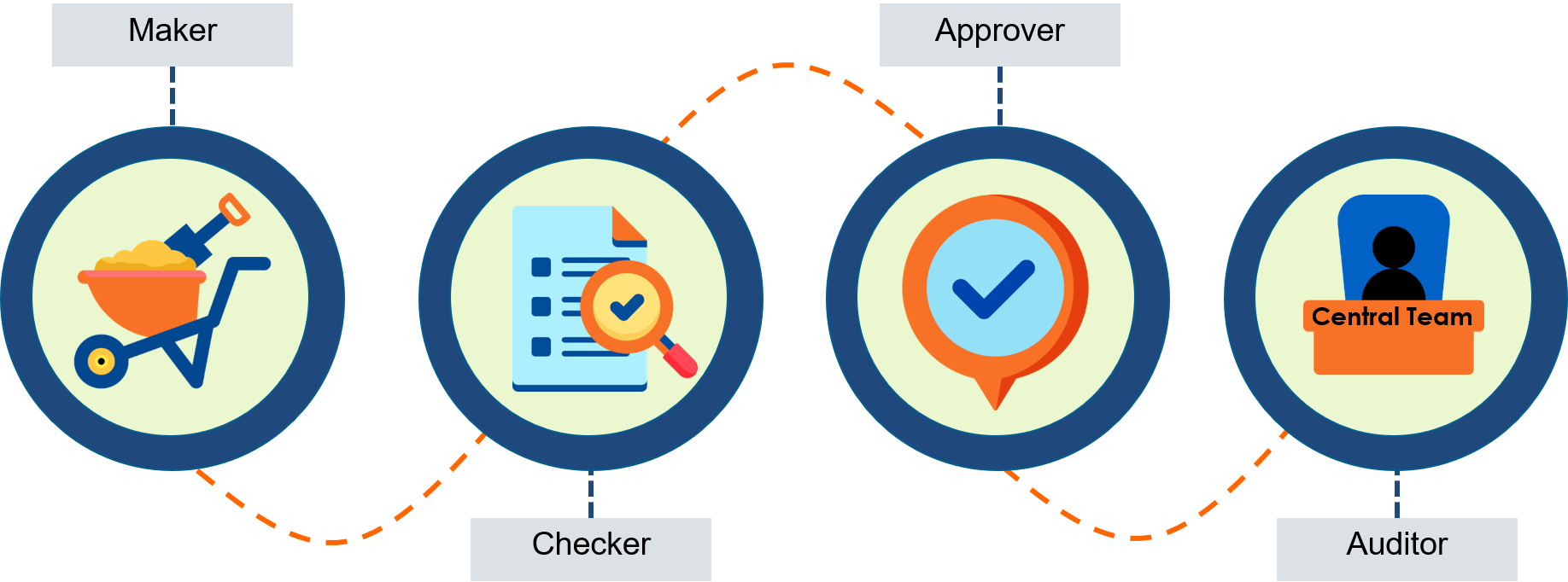
1. Maker:
Maker is the most basic step in quality control but the most significant. The actions of this agent will decide the quality of the product produced. Basically, the contractor on the construction site is the maker and the first one to regulate quality. But the responsibility of establishing a standard method for execution and its limitations are briefed by the auditor.
A contractor is responsible for establishing quality standards, reviewing quality control plans in the pre-construction stage, constructability reviews, material management, inspection schedule, and non-conformance operations such as tracking and corrections.
2. Checker:
Checker is the second stage of onsite execution, inspection, and data collection. The site engineer and supervisor fall into the checker category. Although everything is briefed to the contractor, the site engineer oversees that there are no exceptions made in following the standard practice.
In case there are some unique conditions and changes are expected, the engineer oversees the details and also ensures that the approver has approved the methodology or changes. The site engineer is the one to fill out the checklist and provide necessary photos and notes on the topic.
3. Approver:
The approver is the project coordinator or project manager. He is in charge of every operation that takes place and also ensures that everything is in order.
The approver is also the link between the on-site quality control team and the central team who sets standards.
The approver communicates between the central team and the on-site team. He can also help in identifying failing agencies and training needs. Facilitation of standards expected by the work team and core values are circulated by the approver.
4. Auditor:
An auditor is a member of the central quality control team. The auditor oversees multiple sites and has the highest authority in the system. The auditor has the power to stop any ongoing activity or activities further to be conducted if he doesn’t find the quality satisfactory. These checks are done at regular intervals for every construction site.
For the checklist to pass dual approval of both approver and auditor is required. If quality is questioned by the auditor, the onsite team needs to verify and reconsider doing checks again.
Why does dual approval matter?
Human errors are natural but frequently repeated. Hence, to bring another set of eyes to inspect the quality of operation. It helps in avoiding any unintended errors or deviating from the process.
Here the approver makes a request for an inspection from the central team and gets approval. The central team member is an auditor and is experienced in getting the quality correct to its very small detail. The advantages of dual approval are as followed:
- Reduction of degraded quality
- Identifying training needs
- Establishing of standard procedures
- Reduction in internal fraud
- Establishing clear accountability
- Transparency in system
- Increase in the prestige of the company
- Establishing a central quality control system.
- Early detection of problem
- Reduction in rework and wastage
The essence of the blog:
Having an extra set of experienced eyes overlooking the eye reduces the chances of a small mistake turning into a big accident. But this also makes clients aware that the data provided to them is double-checked and they need not worry about construction quality. This also brings transparency to the system and inter-relations between the agency providing the facility and the client.
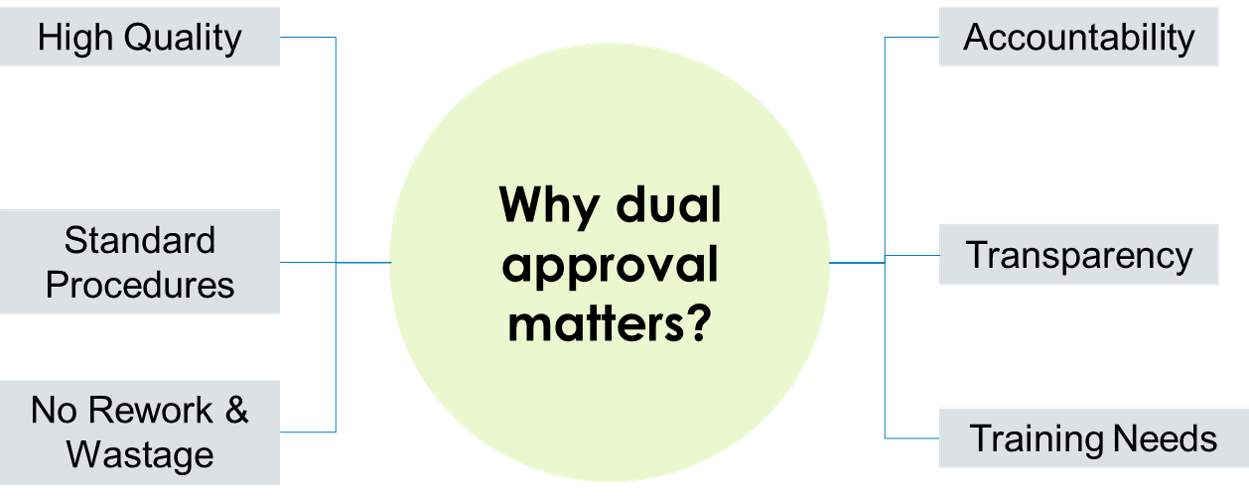
Now when we talk about this dual approval, we need to talk about how digiQC enforces the dual approval. But for this first, we need to understand how to make a quality control checklist. These checklists as we discussed earlier are frameworks to assess quality when audits take place. digiQC offers quality control solutions for Project owners, contractors and consultants with the smart features and high-end digital systems that are proven to improve your quality management.
There’s more. Wealso have a quick guide for the quality management system you can adapt with digiQC. Read it by clicking here: Quality management in construction—An Overview