There is always a hierarchy or methodology followed to complete a certain task. When we define a system for controlling a process, we essentially create standard guidelines to follow or certain steps to endure that the execution has taken place to produce a quality product.
Since the tagline of digiQC is “focus on quality,” it certainly has adopted a methodology for quality control. First, we will discuss why quality and all of quality management are important.
Delivering quality is important for customer satisfaction and maintaining a reputation. The effectiveness of quality control depends on various factors such as quality process, actual quality control, and its analysis. Quality control processes and strategies are established to identify any deviation in quality as per specification, and improvements are made based on the available history quality data.
Since quality is of utmost essential and is the very fabric of the organization, we must first understand the types of quality control systems prevalent in the construction industry.
1. Type of quality control system
Today when digitization has reached the construction industry, it can also be adopted for quality control systems. The way quality control system is established in any organization plays an important role, and these quality control systems are mainly centralized quality control systems, decentralized quality, or Hybrid quality control systems. Let’s understand each quality control system in brief and which shall be adopted to get the best result for your organization.
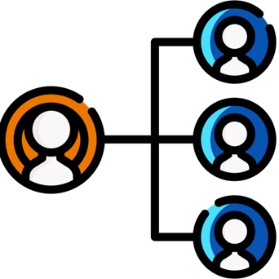
2. Centralized quality control system:
It is a system where the Quality head of the organization manages and controls the quality process. This head is responsible for setting standards that best suit the organization. This system set by the quality head is followed in every project of the organization. This Quality head has a team that is responsible for this quality process is followed the same is monitored, and improvements are made based on the analysis.
For example, when the centralized system is applied for the construction organization, then the Quality head along with the team standardizes the quality process in the organization. Once the project starts, this process is implemented in the project through proper training and implementation process. This process is monitored by the quality team, and reports are prepared. These reports are then analyzed, and based on that process; improvements are made if required. Due to highly qualified personnel at the organization level, Project quality improves.
3. Decentralized quality control system:

A system where responsibilities are scattered across the system
and are individual units controlling the processes. Its mainstream idea is to lead a team of subject matter experts for each process. In such cases, synchronization and smooth workflow become problematic.
For example, in an organization where there is no centralized quality control system then, once the project starts, the site project/quality manager sets the quality control process as per his best knowledge and experience. This quality control process is generally not monitored, and so there is no scope for improvement. This system can be effective or not depending upon the knowledge and experience on-site Project manager/quality head.
A hybrid approach for quality control:
The hybrid approach is a combination of a centralized and decentralized approach. It utilizes a central approach for important global processes such as checklist formation and uses a decentralized approach for managing local approaches. If not done properly, this approach brings out combined problems of both systems.
4. Implementation of the centralized system using digiQC:
digiQC is a construction quality control tool that can be used to digitize quality control through a centralized quality control system. This centralized approach through digiQC is divided into levels to ensure proper flow of information and process is followed. This will give quick reaction time, better communication, and coordination among the organization and enhance the quality of the organization.
Following is the hierarchy in the digiQC system
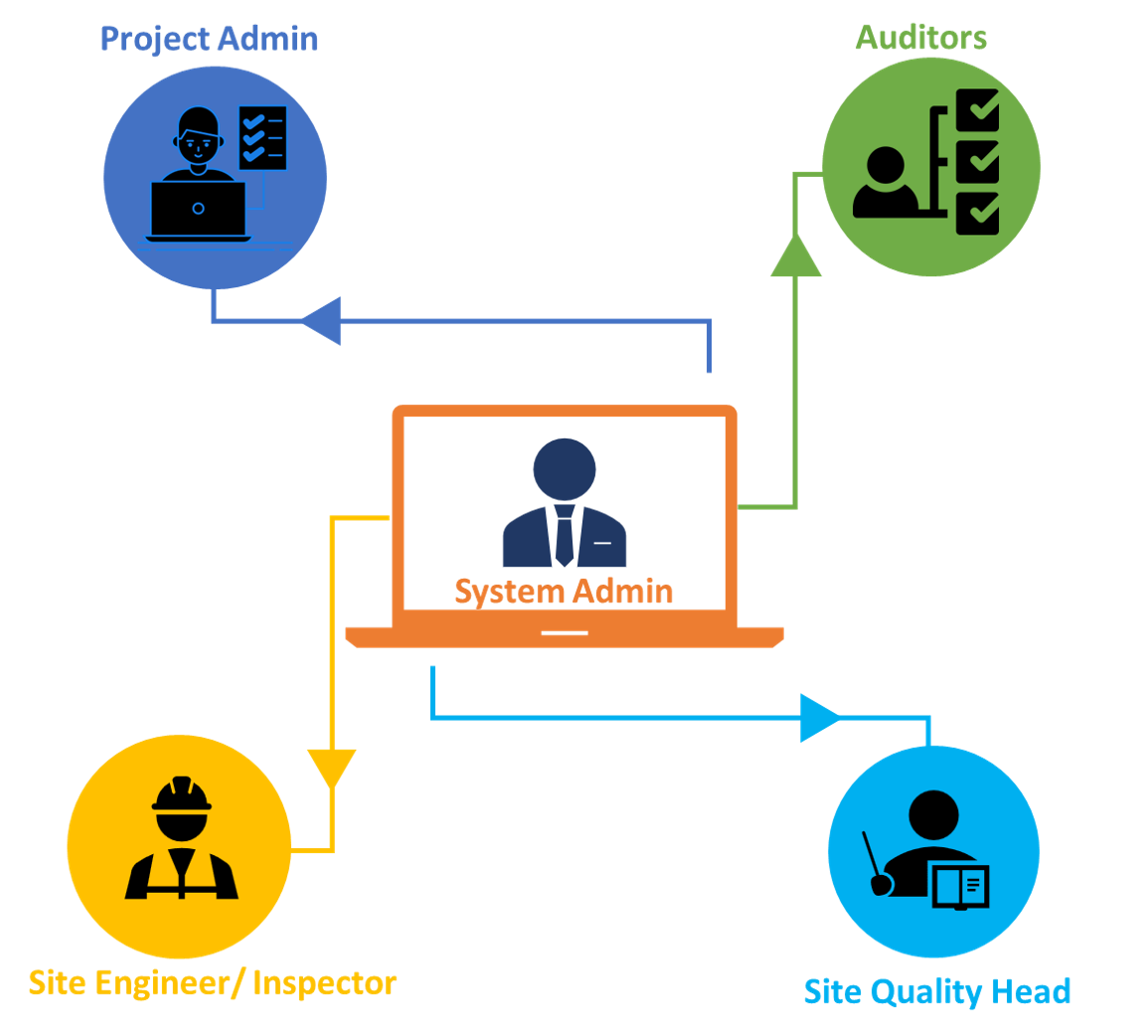
In digiQC, the system admin setup the organizational data. This organization includes organization users, agencies, and checklists. Project is created for the organization by system admin where he can restrict the area of quality control through location radius restrict. This ensures the inspector has to be on-site while doing quality control. Also, the System admin can make photographs compulsory for particular checklist points for which the inspector has to take photographs through a camera only and ensure he was on-site during quality control.
Once all this setup is done by the system admin, the project admin for the project can import all the data at the project level from the organization level. This will ensure all the standardized data is used. If project-based modification is required in checklists, this can be done by the project admin. Project admin can also restrict which checklist an inspector can view and inspect, ensuring only the subject expert can only do the specific inspection.
Once all the project setups are done inspector can do the inspection in a mobile application. He can set reminders for the agencies and the project users for the next stage also. In case there is a QC failure, an automatic email is sent to agencies and project users for quick communication and decision making.
Remote approval can be set up for important checklist stages, or an expert view is required. The internal or external auditor is also an integral part of a quality control system.
All the inspections done by the inspector are stored in the cloud server of digiQC. All this data can be analyzed and can be used for decision making, root cause analysis, training need identification, and system improvement.
5. Advantages of using the centralized system through digiQC:
The centralized system offers a more composed approach for organizations to implement quality control. There are several advantages to the system:
Experts with diverse skillset: This helps in ensuring that creative solutions are provided with technical feasibility. The diverse employee portfolio helps in ensuring that there is no adverse impact on other factors.
A hierarchical chain command: The whole workforce is given a chain of command. This gives the scope for better communication and ensures that problems are reported immediately. It also ensures that imposed rules are considered seriously and strictly followed in order to achieve outlined quantity.
Quick implementation: This is added benefit of the central system in case there is a sudden change in the plan of action. This is considered a benefit as it reduces rework.
Risk mitigation & quick response: Supposedly, there is an occurrence of problems due to either human error or technicality. The response time is quick due to dashboard availability.
Cross-functional training: Cross-functional training is an approach that gives a unique perspective to the problem at hand.
Centralized data source: Centralized data sources store and manage all the documentation work done for quality control. This helps in ratings, responsibility upholding, and accountability for losses in the time of failure. It also records & stores data and can be retrieved in times of crisis immediately.
Standard procedures & checklist: Setting up a standard checklist project-wise as per the demand. This also helps in making the process standardized.
Frequent review and verification: The review process is easier and can be done remotely. Also, verification can be easily done in real-time.
Cost efficiency: Cost efficiency is achieved using a centralized system because it increases efficiency & productivity.
Real-time quality control: Real-time quality control approach is applied using various technology-based parameters. This allows quality control to take place in real-time with data stored in cloud storage software.
There are also some drawbacks to a centralized system. It affects the workforce’s ability to improvise and implement the techniques & develop their scope of work. This issue can be resolved by taking steps such as brainstorming sessions with all levels of the workforce. This boosts their confidence by allowing them to express their ideas in the workspace and assuring them that their voice is given importance.
Conclusion:
The centralized system is a very effective method with the very least drawbacks. This drawback can be resolved and can make the centralized system faultless. But when a centralized system is combined with digital tools like digiQC, a centralized system becomes more efficient and reliable. Thus, one must consider taking aid of such technologies to improve their quality process and can increase their goodwill in the market.
Since we discussed the quality control system, we should also understand that this system, along with digiQC, also helps in finding the root cause of these systems. Root cause analysis is certainly a great quality management tool that can be used to mitigate risk and avoid the same kinds of problems in a repetitive manner. Thus implementing a quality control system with digitized tools such as digiQC can help us achieve supreme quality, prestige and customer satisfaction.
Still looking for details on quality management? Read the curated blog series from digiQC: Quality management in construction—An Overview to get the complete picture of quality management.