Unpredicted problems occur in construction every step of the way. But these are generally fixed with temporary fixed which is similar to treating symptoms, not the disease. Instead, root cause helps you in identifying the problem from where it originated and contributing factors that lead to the occurring problem.
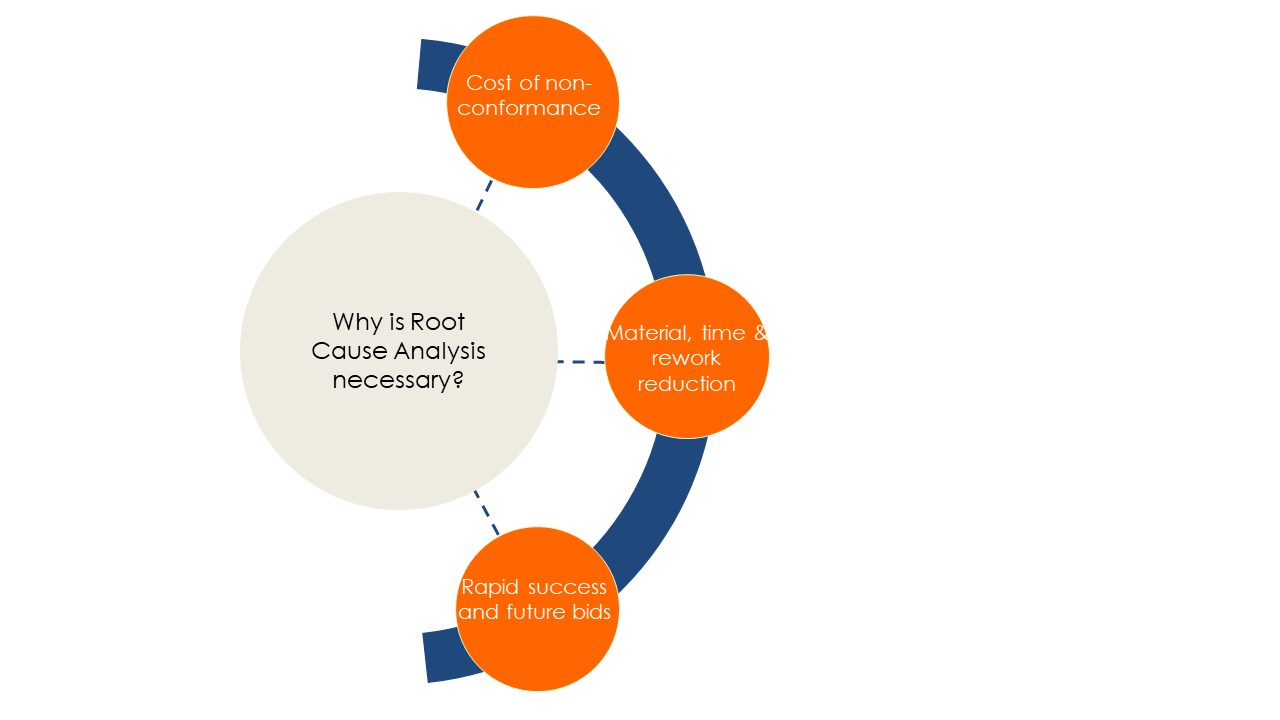
But first, we need to understand what root cause analysis means in quality management, what are the requirements to conduct root cause analysis and how it should be conducted? The following blog sheds some light on these issues.
What is root cause analysis?
Root cause analysis is done to reduce the cost of non-conformance. It’s addressing to the tangible problem that can be solved by applying a continuous improvement methodology. It is an investigative procedure that can help in reducing recurring incidents, near-misses, quality problems, human errors, production errors, and major accidents.
It can be divided into two parts: cause and effect. The effect is the incident that took place that doesn’t comply with the standards established. The cause is the circumstance or set of conditions that lead to a ripple effect.
Saying this, the root cause may uncover that a single set of parameters set in motion a chain of effect that resulted in different non-conformance costs.
How to perform the root-cause analysis?
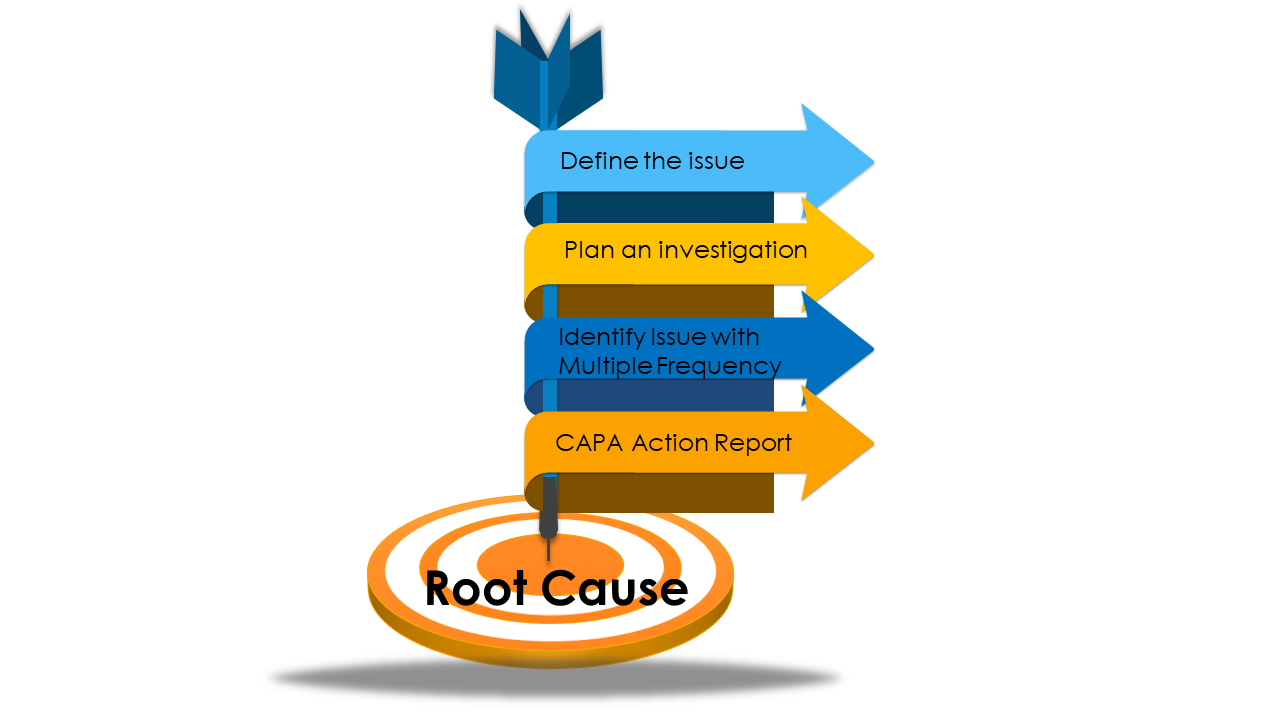
1. Define the issue
At this stage preliminary, we define the problem statement and scope of the investigation. Here, nomination for an investigation team is done, roles are appointed and data collection techniques are identified.
Here problem statement is defined and the work required to identify the root cause is enforced. If this is not done and the scope of work is not defined one might find themselves in loads of data and the investigation will be inconclusive.
Take an example of the failure of concrete to achieve its target strength. This example will be used for the rest of the process to facilitate a better understanding of how root cause analysis should be done.
2. Plan an investigation
At this stage, a detailed list of activities to be executed for identification is stated. What information to be acquired and from which data source is analyzed, the flow of information for the particular activity and agencies involved. Primary data collection starts at this stage and is later on extended for root cause analysis.
For the failure of concrete, information needs to be acquired such as materials used, their specification, the method used for concrete, and the agency providing the service. Other data input points can be recorded from checklists.
3. Take immediate corrective measures
Although doing roots cause analysis for finding the problem at its root, immediate corrective actions are required. Near miss event or an accident requires immediate attention. In case of failure of concrete activities that increase the structural load on concrete can be withheld until further clarification or notice from the structural team.
4. Identify issues with multiple frequencies
Identifying issues with multiple frequencies is another term for searching through a list of viable options to find out the cause of origination. The list of bullet points that can help in recognizing the root cause:
- Identify the inspector
- Identify the primary agency involved.
- Identifying the checklist
- Raw materials and machinery check
- Methodology variation and human error consideration
- Was human error repetitive? Was workmanship questionable? Helps in identifying training needs for a particular agency.
5. Record the data
With all the data identified in the previous stage, sort and filter the data for differential analysis. The data that is recorded should be stored in a proper format. Also, it should be retrievable in case the same problems arise with a different form of complexity.
Analysis should be done to identify the point of origination and the root cause behind the problem. At this stage it shall be root cause should be concluded and moving forward focus should be on preventative measures.
With digiQC, data storage and data retrieval is a very smooth process as a result of the cloud storage option.
6. Plan corrective and preventative actions
Now, two types of action can be taken to resolve the problem. First is corrective action that focuses on eliminating the issues that can be introduced to already existing failure whereas, preventative action focuses on eliminating the root cause and thus reducing the cost of non-conformity. For failure of concrete, corrective action can be strengthening methods, Non-destructive testing to confirm failure, or recasting the elements. Preventative action taken for failure should be addressed to the issue specifically. If materials failed then replacement of materials is required. It can vary from changing casting methods, training labors to ensure mixed proportions are being followed or simply just following IS standards of post-construction such as doing proper curing as stated.
7. Evaluate success and continuous improvement methodology
Now, both actions in progress evaluate success, outcomes, and changes brought on by those actions. If the results are not satisfactory one should return to stage 4 that is identifying issues with different frequencies. This will lead to continuous improvement and ensure quality construction is being provided.
The essence of the blog
Thus, the article sheds some light on how root cause analysis should be done and how beneficial it is to provide quality construction to clients with keeping budget in mind. Making root cause analysis a widely used construction technique will help in reducing non-conformity costs. Along with this, it can help in saving material and time which will in turn boost the economy for the construction sector.
Before understanding the importance of root cause analysis in quality management, one must understand that there is a dual approval procedure Maker-Checker that digiQC follows. It helps in enforcing strong values of accountability, transparency, and continuous improvement in standard operating procedures.
Running out of time to read? Check out the outline of the exclusive blog: Quality management in construction—An Overview to understand the key takeaways in no time.