In our last story, we discussed the principles of the kaizen approach and how it is applied in the construction industry. Now let's discuss the six sigma principles.
The six Sigma approach is a high quality management approach first used by car production company Motorola. The Greek letter 'Sigma' means deviation. In mathematics, 'Sigma' is used for the term of standard deviation from its mean. Hence six-sigma means six factors contributing to deviation resulting in defects. Six sigma helps in making a product with zero defects.
Six sigma is an analytical and data-driven process that uses a wide range of tools to achieve improvement. This approach aims at reducing variation in processes, in turn providing consistent and desired outcomes. It is a top-down and resource-intensive approach. It focuses on process improvement by controlling the 6 M's of the production process. It has integrated DMAIC Model for continuous improvement. Six-sigma is a highly effective method designed for achieving customer satisfaction.
Principles of the Six-Sigma Approach:
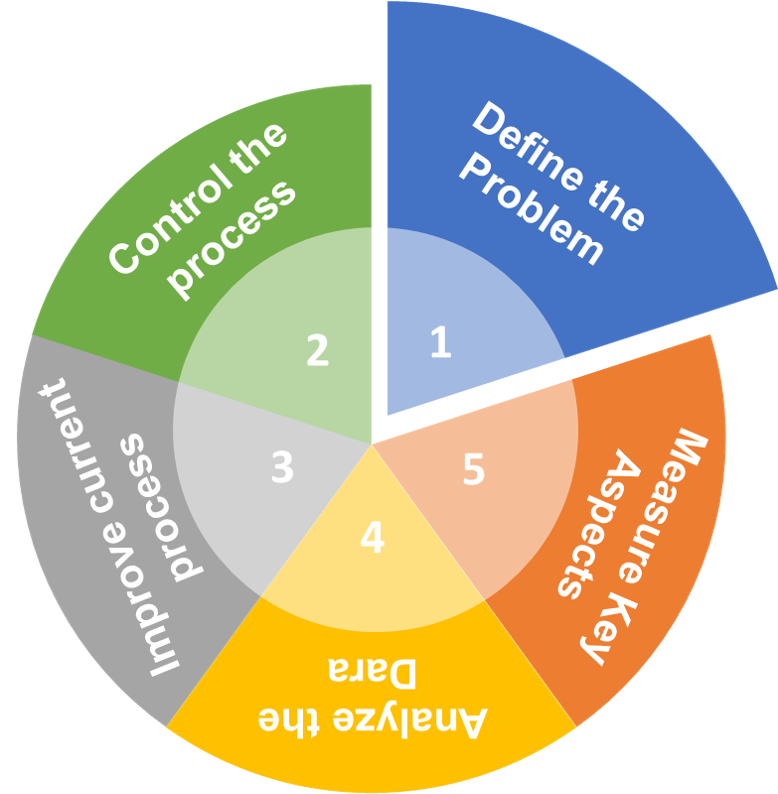
1. Define the problem:
This is the input phase which requires input from the management team. It defines the scope of the project and specifies the problems encountered. Here goals and implementation plans for process improvement are defined. The client's value and definition of quality according to them is also integral input at this phase.
2. Measure key Aspects:
As the name suggests, the main aim of this step is to collect data. As the earlier phase, it is also the input stage. Here key aspects affecting the production procedure are recognized and the impact is analyzed. This stage, unlike the first one, collects data in real-time and analyzes the available data from earlier reports. The data collection plan collects input from different levels of the organization and figures out the factor leading to variation.
3. Analyze the Data:
This stage is completely based on transforming raw collected data into a statistical format. It utilizes different tools for grouping and organizing the data. Some of the tools are fishbone diagram, Hypothesis testing, work breakdown organization, flow charts etc. At the end of this phase, you, the team, pinpoint the factor causing variation. This conclusion is validated through the data analysis and can be cited for variation in the production process.
For example, multiple works done by contractor and checklists and data retrieved shows that the crew needs to be updated on the technology used. This conclusion is reached by considering all the various scenario that affects work condition, from weather to skillfulness & accreditation of the personnel.
4. Improve current process:
Previously done analysis helped in the determination of variation causing factors. Now, the approach demands a rectification in process. This is done by developing a solution or solution set for a problem. Various options can be exercised to improve the current process. The most appropriate method can be selected for implementation on a large-scale basis. This implementation plan is designed to mitigate risk, and specifics such as action to be taken, a person in charge, the person responsible for carrying out the procedure, and the inspection team are also mentioned. This implementation plan is also discussed with the client to increase customer satisfaction and transparency for the successful completion of the project.
For example, the quality control method on-site is conventional and needs upgradation to digital tools. This method needs a clear implementation plan and training. This can only be done by the head of the organization overseeing this process.
5. Control the future process:
The control of the future process is allotted to the responsible party who can efficiently implement the process. Standards are established according to requirements, and verification of benefits and profits is also done. This implementation is also monetarized, and detailed reports are submitted. The salient feature of this step is to hold the gain as well as increase it using new modifications.
The main focus of the Six Sigma Approach – 6 M's
As mentioned earlier, the main focus of this approach is to improve its implementation process. This is done by the principles of the DMAIC Process. But the main focus of these processes is on six control factors that cause variations. These 6 Factors are materials, method, machines, manpower, measurement, and mother nature. These factors cause variations as they fluctuate. Some of the reasons for fluctuations are mentioned below:

1. Materials: Materials are manufactured by various methods. Its content and compositions differ from producer to producer. Now, if the certain method requires a specific type of material to fulfill its basic requirement. The specifications are in it's make & compositions. Now, if the process utilizes different materials, then the desired outcome cannot be achieved. Also, transportation, storage & duration of storage matter in construction materials. For example, cement needs to be stored in a cool, dry place 150-200 mm above ground.
2. Method: Methods are a major cause of variation on construction sites. The method executed by a contractor can be different from another contractor. This can lead to a difference in the quality delivered. Concreting done on-site by a contractor uses accurate measures and uses a concrete mixer, whereas another contractor also uses an automatic mixer, but no accurate measures are used. Then the quality of concrete will differ and can create technical problems.
3. Machine: This includes all the machinery, tools, and equipment used in the construction process. This also includes factors such as the leasing period and renting cost if the equipment is not purchased. This needs critical inventory and needs to be updated regularly. Failure in this can cause disruption of work as the construction site completely depends on mechanical tools to carry out even the simplest of all activities such as lining.
4. Manpower: Labor capital is the most sensitive factor of all. They need to be treated respectfully and paid accordingly. This factor only fluctuates if the rates they are provided are not sufficient. Manpower also includes the management system and human resources required to run operations. It needs a clear chain of command and standards to follow.
5. Measurement: It basically includes the inspection system and standards that the organization upholds in terms of quality. Suppose the inspection personnel is not trained and motivated enough to carry out the process enthusiastically, then it will lead to undesired results. Training also plays an important role in this aspect of fluctuation.
6. Mother Nature: As the name suggests, it includes climatical aspects which are beyond human control. If climatic conditions are unfavorable, all activities will be at a halt. This can be considered while planning a project, but there is always a possibility of variation.
Advantages of the Six Sigma Approach:
Advantages of the six sigma approach are as follows:
1. Increased customer satisfaction. This generally leads to an increase in revenue stream as the idea spreads that the company indulges high standards for quality management.
2. As it is top -a down approach, it is highly structured and logical. It requires solid data backup and proof to introduce a change in the system.
3. The output from one phase is the input for another end. This leads to highly data web, which requires input from each level of the workforce.
4. It reduces the deviation in any process by controlling factors affecting it and organizing the timeline and workflow.
Drawbacks of the Six Sigma Approach:
The disadvantage to this method is that it is a highly complicated system. Thus, a company with an already existing system of quality control might find it difficult to adopt. New companies adopting this system need patience and a strong workforce subordinate to deliver the required results. This is the only drawback to this system, and one might be able to overcome it if all levels of the workforce in an organization are given importance, and their input is considered valuable.
Conclusion:
The conclusion stands that the only way to implement this complex methodology is by adopting a holistic approach for quality management. This method is very efficient and preferred over another method as it considers six factors of deviation. This is a salient feature of this method and adds value to this method. The six-sigma approach is the top to the down approach, which is a standard approach used by construction firms worldwide.
Along with this, there are certain things that we need to keep in mind when we are developing quality control methods. It includes crucial steps such as developing standards checklists, doing root cause analysis, and keeping up with emerging construction trends in the construction industry.
Read more on how these methods can be employed at our exclusive blog: Quality management in construction—An Overview. Keep checking out our blog section for more such helpful topics