The complete guide on the importance and use of IS 10262: 2019
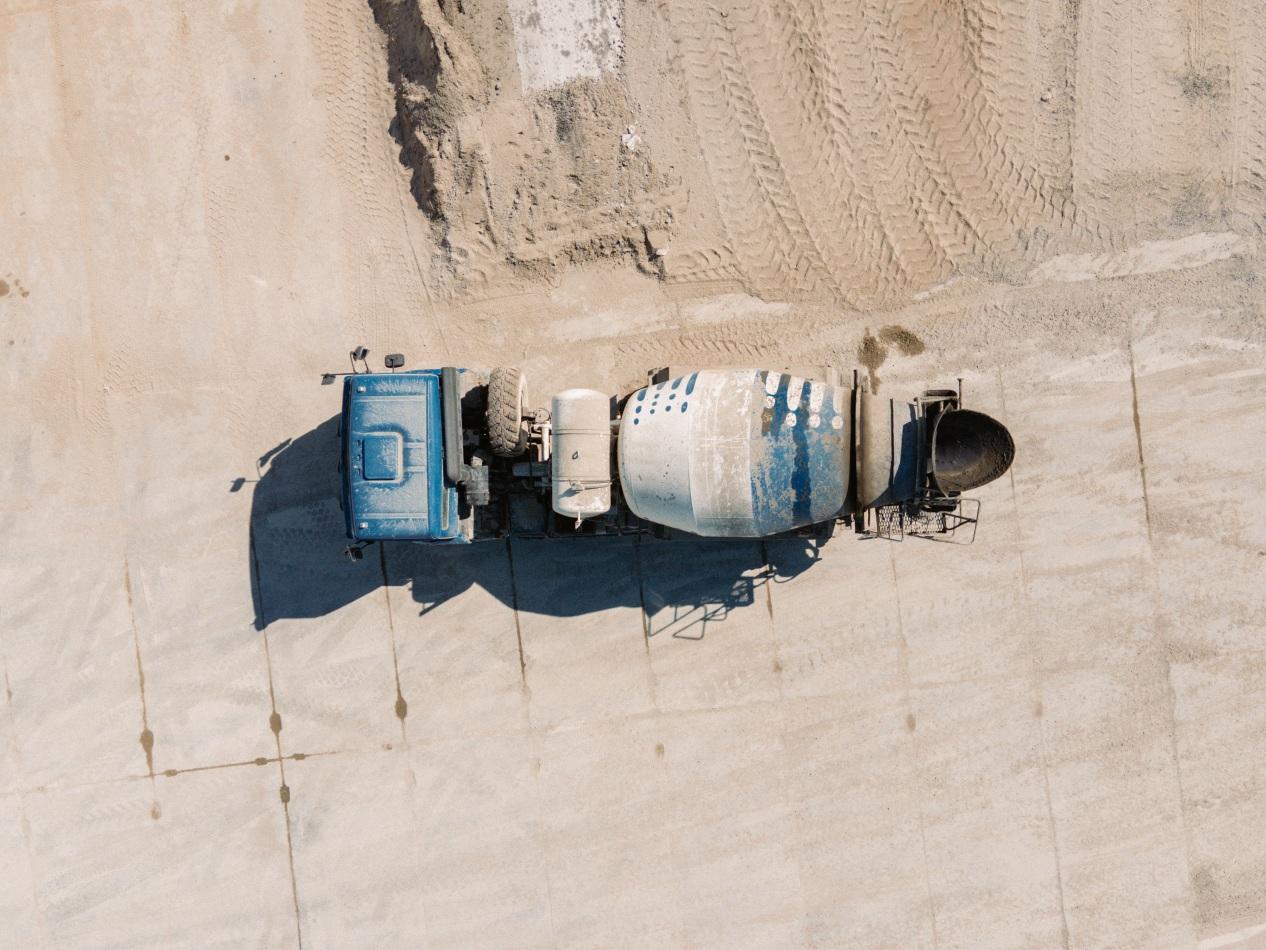
Introduction
What is concrete?
Concrete is a heterogeneous mixture of ingredients including cement, fine aggregate, coarse aggregate, and water. These elements when mixed in the right proportion form a strong and durable material of specific strength once it hardens. The fresh mixture is typically in a liquid state. Only the balanced proportion of the elements can ensure the strength of the hardened concrete.
But what is that right proportion? How to create one? The IS 10262 is your handy guide for reference.
The I.S. 10262: 2009 code provides the most economical and practical combinations of concrete-making materials. The updated edition (2019 ) of the code covers the mix design requirement for ordinary, standard, and high strength, self-compacting concrete, and mass concreting.
The code also mentions the guidelines to include substitute materials that partly replace cement and aggregate. A few popular materials include admixtures, fly ash, GGBS, rice husk ash, metakaolin, and superplasticizers. These are cheap and also do not degrade the quality of the concrete in the concrete mix design. Said so, the question is what is the credibility of the IS code?
Who prepares these standards?
The Bureau of Indian Standards publishes codes like these for the harmonious development of the activities of standardization, marking, and quality certification of goods. These codes are prepared after extensive research done across the country by reputed construction companies and organizations. The IS codes are freely available in public resources and can be downloaded from the internet.
Now, let's learn what IS 10262 is all about.
The IS 10262 gives detailed steps on how to prepare a concrete mix design. If you want to understand the mix design procedure, here is a brief outline of the code:
Section 1 of the code covers the Scope, References, Terminology, Data requirements
Let's say you want to prepare a mix of the grade 75 MPA. In that case, the code asks you to note down the following data:
1) The desired grade
2) Type of cement, and grade of cement (if applicable)
3) Maximum nominal size of aggregate
4) Minimum cement/cementitious materials content and maximum water-cement/ cementitious materials ratio to be adopted
5) Workability required at the time of placement
6) Transportation time
7) Method of placing
8) Degree of site control, if any
9) Type of coarse aggregate
10) Type of fine aggregate (natural sand/ crushed stone or gravel sand/manufactured sand/ mixed sand)
11) Maximum cement content
12) Which chemical admixture shall or shall not be used and the type of chemical admixture and its extent of use
13) Which mineral admixture shall or shall not be used and the type of mineral admixture and its extent of use
14) Any other specific requirements like early age strength requirements.
Once you are ready with the basic data, the code provides steps to prepare the concrete mix design. Here they are:
Step 1: Calculate target strength for Mix Proportioning
The first step in the design process is to determine the type and compressive strength of concrete required for the project. This will depend on the intended use of the concrete and the design requirements of the structure.
This is the safety factor; the minimum strength we want our concrete mix to achieve.
Step 2: Calculate the Standard Deviation for each grade of concrete separately
Requirement: Minimum 30 Samples.
Standard deviation suggests the degree of quality control of the concrete. Less deviation signifies better quality.
Step 3: Mix Design for ordinary and standard concrete grades
Selection of Mix Proportion:
1. Select water-cement Ratio
2. Estimate air content
3. Select water content and admixture content
4. Calculate cement/cementitious materials content
5. Estimate the coarse aggregate proportion
6. Combination of coarse aggregate fractions
7. Estimate fine and coarse aggregate contents
8. Trial mixes
The code suggests four trial mixes provide sufficient information, including the relationship between compressive strength and water-cement ratio, from which the mix proportions can be finalized, such that the strength and durability requirements are also satisfied.
If the trial mixes do not meet the required strength and other performance criteria, you can adjust the mix proportions and conduct additional trial mixes until the desired properties are achieved.
The process to estimate the mix design is simple and could be learned by practice. And if you already know the process, you might find it easy to also create a high-strength mix proportion. If not, section 3 of the code is for you.
Section 3 of IS 10262: 2019 gives details about the Mix Design for High-Strength Concrete
High-strength concrete is concrete that has a characteristic compressive strength of 65 N/mm2 or more.
The process to determine the mix for high strength is similar to that of design for ordinary concrete. The difference, however, is the use of superplasticizers and a low water-cementitious material ratio (w/cm)
Here you can use cementitious materials like:
Fly ash, silica fume, ground granulated blast furnace slag (GGBS), or metakaolin as cementitious and pozzolanic ingredients in high-strength concrete.
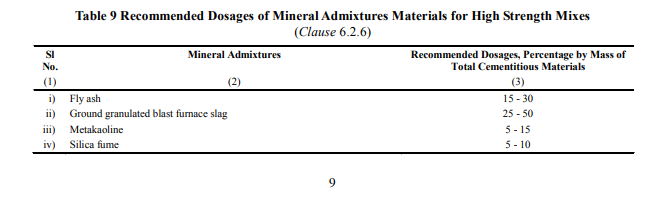
The steps to mix design of High Strength Concrete are similar to that of ordinary mix and are covered in the code under section 3.
Section 4 of IS 10262: 2019 - Self-Compacting Concrete
Self-compacting concrete (SCC) is a flowable, non-segregating concrete that fills uniformly in every corner of formwork under its own weight. This ensures that reinforcement is not disturbed and that the concrete remains homogeneous.
Self-compacting concrete (SCC) is a revolutionary product that can be used in a variety of precast concrete applications or for concrete placed on site. SCC is perfect for casting sections with highly congested reinforcement and in areas where access to placement and consolidation is restricted. It can be manufactured in a site batching plant or in a ready-mixed concrete plant, delivered to the site by truck mixer, and placed either by pumping or pouring into horizontal or vertical forms.
The steps to mix design of SCC are similar to that of an ordinary mix and are covered in the code under section 4.
Section 5 of IS 10262: 2019 - Mass Concreting
Mass concreting is needed to construct massive structures. To prevent cracking from occurring in large cement structures, measures need to be taken to compensate for the generation of heat from hydration. By ensuring that the volume change is minimized, it is possible to avoid excessive thermal expansion and related damage.
Mixing proportions for mass concrete is an important part of achieving the desired properties. By selecting the proper mix, you can ensure a strong and durable product with good permeability and workability. Additionally, by choosing the right materials, you can minimize temperature rise after placement.
The steps to mix the design of Mass Concreting are similar to that of an ordinary mix and are covered in the code under section 5.
Once you have your design ready, you are supposed to tabulate the data in a report as mentioned in clause 5.8.1
So, you are ready with the mix design. You can now adjust your batch plant inputs accordingly to get the concrete of the desired grade.
If you are still in doubt about specific mix design cases, refer to Annexure of IS 10262: 2019. There, you will find sample mix designs for each concrete type. There are 6 designs covered within Annex A to F
Okay, what more? A good mix design increases the quality of hardened concrete and creates a durable structure.
Benefits of using IS 10262: 2019
There are several benefits to using IS 10262:2019 for the design of concrete mixes:
1. Consistency ensures a reliable concrete mix.
2. Quality control helps to ensure that the concrete meets the required specifications.
3. Possible to achieve the required strength and other properties of the concrete at a lower cost.
4. Help to ensure the safety of the concrete mix, which is particularly important for the construction of critical structures like bridges and dams.
One of the key features of IS 10262:2019 is it encourages the use of locally sourced materials in order to reduce the environmental impact of transportation and to promote sustainability.
How you can use IS 10262: 2019
Concrete Mix Design provides a scientific approach that helps predict the desired strength of concrete. A sane proportion thus assures the strength, durability, and workability of the mix.
The standard is applicable to the design of concrete mixes for use in all types of construction, including residential, commercial, and industrial projects. It is also relevant for the design of precast concrete products, such as blocks, pipes, and precast beams and columns.
Now that you've mastered the quality, consider upgrading the tools you use for your construction needs.
Digitize your Quality Audit and Quality Control needs. Reduce paperwork and save costs by automating your processes. You can consider using our mobile-friendly construction quality control app that has an in-built checklist to ease your construction site compliance work.
If you are interested in knowing how you can be smart in providing quality checks, schedule a free demo today.