We take risks in performing even a fairly simple task. Running an errand or just choosing a piece of clothing for a particular function. Mitigation strategies for such are simpler than what a construction industry faces.
The construction industry, unlike any industry, has more uncertain criteria and stakes. This makes it more vulnerable to chances of failure. Each project is unique and comes with its challenges & outcomes. Managing personnel requires risk identifying & critical thinking capacity to mitigate risks. However, it's one of the trickiest parts that is conceivable through planning & risk mitigation.
But first, lets us understand simple terminologies of risk management and why is it required:
1. What is Risk Management?
Risk is the potential event that can cause a project to fall flat by failing to meet its outlined expectations. Generally, the risk is allocated to the best-equipped party to administer it and execute the rectification process.
Risk management is the identification, evaluation & prioritization of risk followed by coordinated & economical use of resources to control the probability or effect of a hazardous event. It is a process of augmenting the acknowledgment of changes that can be taken to avoid a major catastrophe.
2. Why is Risk Management Required?
Risk management is a critical aspect of developing a project. Elimination of this process results in an overrun in the budget, decreased productivity & profitability, safety risk, and delayed project timeline. Despite the approach to avoid risk completely, we can gear up using risk management tools to minimize its extent. Digital software & project management solutions provide easier and more efficient risk alleviation processes.
3. Types of risk affecting construction procedures:
To full grasp the severity of risk management, first we need to understand different type of risk affecting construction activities. There are four major categories of risks affecting the construction activities:
1. Financial Risk:
Anything that can affect a business's finances is considered a financial risk. Financial risk is experienced in three main areas: excessive labor, equipment handling & change in cash flow.
Cash flow, often termed as liquidity of funds is the most influential factor in the financial risk management of a developing project. It is referred to as the number of money equivalents that move in or move out of a project at any given type. Negative cash flow indicates financial problems that can lead to a developing project's abrupt stop or collapse. Cash flow is affected by many aspects such as interest rates, labor charges, material & equipment costs, along with changes in legal rules & regulations.
Labor charges account for a major portion of the contractor's billing. If the project has labor-intensive work, the financial stress of making a payment every week or two can make cash flow difficult.
A wide variety of tools & equipment are required for different construction processes. Planning & handling the equipment required is a huge task. If not done properly, it adds up to a budget overrun. Equipment management needs to provide maximum benefit at the minimal expense of the company's resources. This is a prerequisite for the timely completion of a project that ensures its financial stability.
2. Contractual risks:
Contractual risk affects a project at either the managing level or during the risk rectification process. While the signing of the contract, allocate the risk elimination & rectification process to the party best situated to control risk. Allocation of risk in the contract bid process is the employer's call. Fair and balanced allocation of risk defines the relationship between the parties and its effect on the project.
For example, in design, risks are allocated to the employer as he can coordinate with the project designer to minimize design errors while the contractor is generally undertaking primary job site risks such as bodily injury or property damage during the contractor's operations.
Also, these risk allocations & citations should be mentioned clearly in the contract, and no foul play shall be made. During these crises, the losses should be incurred by the responsible party and aid the process.
3. Operational risk:
This type of risk is classified into two categories so far.
The first matter on hand is coordination risk & communication troubles. Lack of coordination results in catastrophic failure. Coordination is important between contractors & subcontractors as well as among the managing authorities. To prevent such hurdles, proper planning & management should be done. Layout & timeline involving different activities should be prepared & circulated for understanding & sequential planning for a smooth workflow. Often, a language barrier between highly trained professional & regional workers & task force leads to disruption of the work cycle creating havoc on the worksite.
Second and the significant risk implied in the disappointment of delivery of quality work. As quality control is a highly definitive process in the success of a project, the risk involved here is also more significant than in others. Failing to provide the quality assured means rework & wastage of valuable resources. Rework & wastage incurs financial & time loss and jeopardizes the enthusiasm of the workforce deployed in the field.
4. External risks:
External risk widely categorizes legal risks & risks related to different laws & regulations placed by government authorities. These risks involve giving possession of the completed project, failing the quality control measures & late deliverance of the completed property. Different laws & regulations are set to uphold the privacy of the people living nearby & to protect against environmental hazards. These are very sensitive matters and require critical planning in advance. Violation of some laws results in the seizing of property by government agencies & imposing heavy fines to the individuals or companies involved in the matter.
As we have seen, these factors affect the organization in the most influential ways; the solution to this is a simpler one. It is to shift from conventional ways to advanced digital tools which are easier & accessible to the construction industry in upcoming days. These tech-savvy tools have a simple interface & make a smartphone a guide to quality improvement.
4. How is Risk Management Done?
A simple procedure is to be followed during risk management. It involves these basic steps:
- Identify the risk and analyze the frequency of occurrence.
- Make contingency plans & it's effect on other activities.
- Decide who will be held liable and will bear the expenditure due to failure.
- Early planning & management can help in reducing the likelihood of failure having the same conditions
-
5. Quality Risk Control through Digital tools:
The construction industry, formerly known as the "brick & mortar" industry, is entering the digital stage. The construction industry is reshaping itself in response to several factors such as client's expectations, new technological capabilities, adoption of digital tools, etc.
The launch of large infrastructure projects is one of the main reasons why digitalization has accelerated in recent years. The use of modern technology gives opportunities such as real-time data collection, dematerialized & in-situ updates, accelerated progress & incident monitoring, and connected workforce & automation.
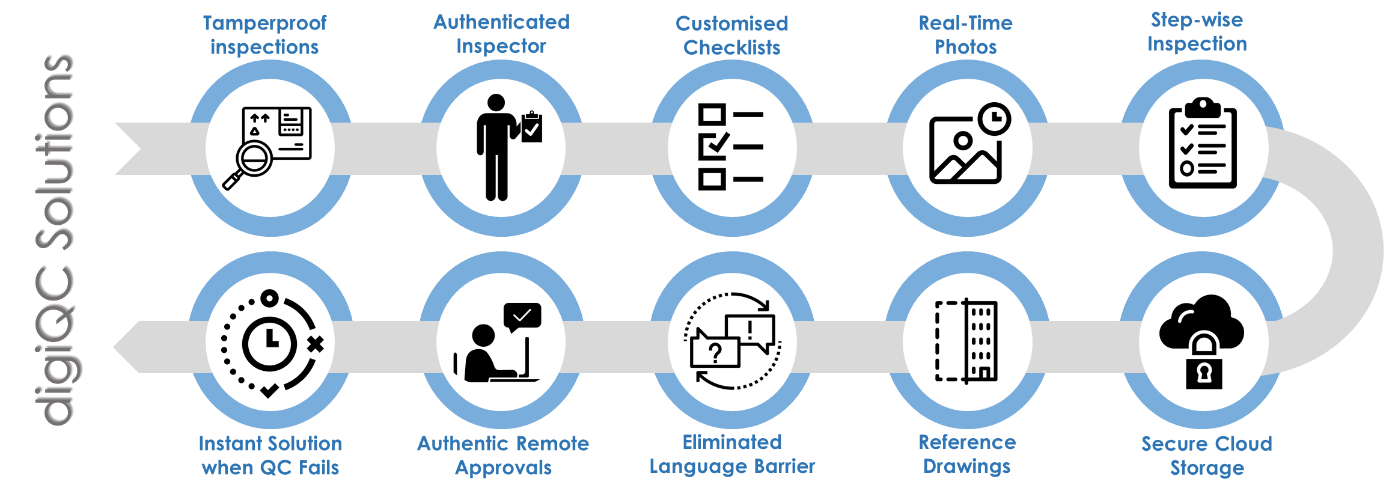
digiQC provides a variety of solutions in regard to the high-quality control approach. This is through a wide range of significant programs coordinated & placed in software that helps from planning until the execution is completed. It provides quality risk control by controlling many unrequited factors that affect the quality of a project & are very hard to achieve using ongoing practices.
digiQC is a software that uses a cloud-based system for storing data. It provides an interface to set up quality control measures for managing authorities. Here, all data is recorded and stored by on-site quality control personnel. As a result of this, it provides tamper-proof documents with real-time photos and drawings. This is also accompanied by a series of checklists sorted for specific activities. Also, the person performing data input is recorded. This helps in risk control procedures when a responsible party is to be notified. Authentic and remote approval is available on web modules in case of carrying an activity involving quality risk, and experts on site are not available.
It notifies the managing authorities instant in case of failure of QC. This helps in the immediate deployment of risk contingency plans and the rectification process. This instant solution providing capacity generates reduced financial risk and budget overrun due to a delayed timeline. Also, all workforce levels are deployed, giving them a fair chance to help in risk mitigation measures.
Conclusion
In the end, we can understand the importance of risk management in the construction industry. Suppose factors affecting it are controlled and supervised along with management & risk contingency plans. In that case, it can lead an organization's way in the marketplace & help them build a strong portfolio of success.
Looking for more ways to improve your organization’s success rate? Head straight to the blog on Construction industry—An Overview if you want totake a look at different practices you can adopt, along with much more details!
Best construction management practices that are prevalent in the construction industry are taken up by my colleague in the following story.