As we advanced into modern development of construction, there was a rising call for efficiency across its phases, which ensured a swift progress in a project’s performance. Quality management came to answer that need of the hour with an empirical, strategy-based system that helped in overseeing all the activities and task involved in the execution of a project. Performed both internally and externally, a quality management system is a project’s best route to ensure on-time completion, reduce risks and achieve the client’s satisfaction at the end. It includes:
- Quality Planning
- Quality Assurance
- Quality Control
Each and every one of these activities in Quality management are elaborate and enabled by a number of strategies and techniques that have proven to be effective. Moreover, the processes in itself come from a set of comparisons, dos and don’ts and more about what-why-how of its methodologies that are too big to fit into a blog. Worry not, we are making it simpler for you!
Here is a quick look into A-Z details of quality management in construction:
- What is Quality Management in Construction?
- What is the difference between QA and QC in construction?
- How to Measure Quality in Construction Projects?
- 3 High Level Quality Management Approaches In Construction Industry
- Kaizen Approach for Improving Construction Quality process
- Lean Approach for Improving Construction Process
- PDCA Cycle for Improvement of Construction Quality Process
- Six Sigma Approach for Improving Construction Quality Process
- Introduction to Four Continuous Improvement Methodology in Construction
- How to do Root-Cause Analysis for Quality Data
- How to create Quality Control Checklist
- Centralized System for Quality Control Process
- 10 Tips for Quality Control in Construction Project
- How to Write a Construction Quality Control Plan?
- Maker-Checker-Approver-Auditor Quality Control Process
- Best Quality Management Practices in Construction Industry
- A guide to improving and elevating your third-party inspections for quality
- Why Inspection and Test Plans (ITPs) are critical for your construction business
- 10 Factors that Affect Construction Quality Management
1. What is Quality Management in Construction?
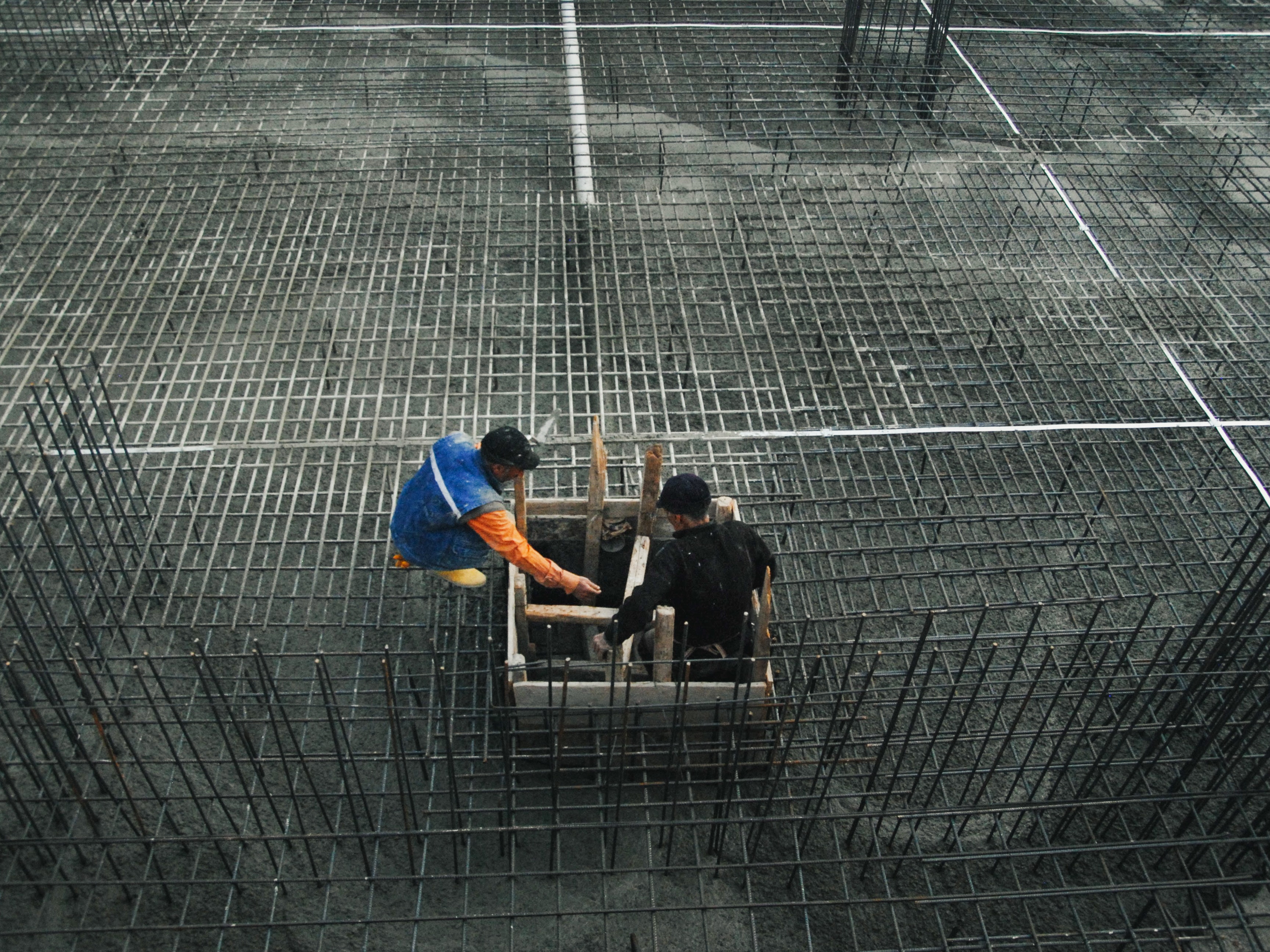
Introduction
A key to achieving success is assembling a stable and strong management team. Quality is never by chance; it is the outcome of intelligent efforts that have to manage.
The essence of quality management is to apply the knowledge and make it productive to achieve the desired quality. A theory of Total Quality Management (TQM) is necessary for the modern construction era as quality has become a parameter we evaluate or evaluate by others.
Numerous questions like what is it, how it is measured, how it is controlled, how to improve it, etc. must be answered to get the required quality. Quality management is often the complete process that answers all such questions.
Takeaways
Quality management is an essential part that must be defined well in advance and abides by throughout the project life cycle to achieve the aimed quality and match the required standards. Some adopt continuous improvement methodology as total quality management approaches to yield higher results.
Achieving the quality management objectives has many benefits but none more beneficial than building a solid reputation in the market in the construction sector. There are many solutions to help you optimize the construction quality processes, like the software solution at DigiQC for all your jobs to meet the highest possible quality standards.
People who are not used to quality always chase the quantity. But they often miss the fact that quality is the best business plan and the best way to reduce the cost and save time for repairs. Quality is a great investment option.
2. What is the difference between QA and QC in construction?
Introduction
Quality is always the result of excellent work without compromise. Having this quality in place throughout the project life-cycle generates the need for quality management. And to simplify the process of this quality management, it is further branched into Quality Control and Quality Assurance.
Quality Control (QC) and Quality Assurance (QA) are crucial parts of the quality management of a construction project to have a quality product or service. These terms are often used together by professionals involved in the construction sites and are often wrongly used interchangeably.
The ideas of control and prevention are often confused with one another. Quality control and quality assurance are inseparable terms in managing quality on a construction project.
However, these terms refer to distinctly different activities on a construction site. Read till the end to learn the difference and the need to identify this difference.
Takeaways
QA and QC are independent terms and cannot be interchangeably used. QA is process-oriented, while QC is focused on the end product. Both of these are important in successfully managing quality on a construction project.
Suppose your layout plans with no assurance of it being followed or considered; the quality goals cannot be achieved. Also, if you inspect or test without a plan, you can sometimes miss the complete picture. Therefore, it is essential to balance and juggle both quality management functions.
To conclude, it is essential to know that quality assurance does not eliminate the need for quality control, as QC is necessary and should not be compromised at any stage of quality management in the construction project.
3. How to Measure Quality in Construction Projects?
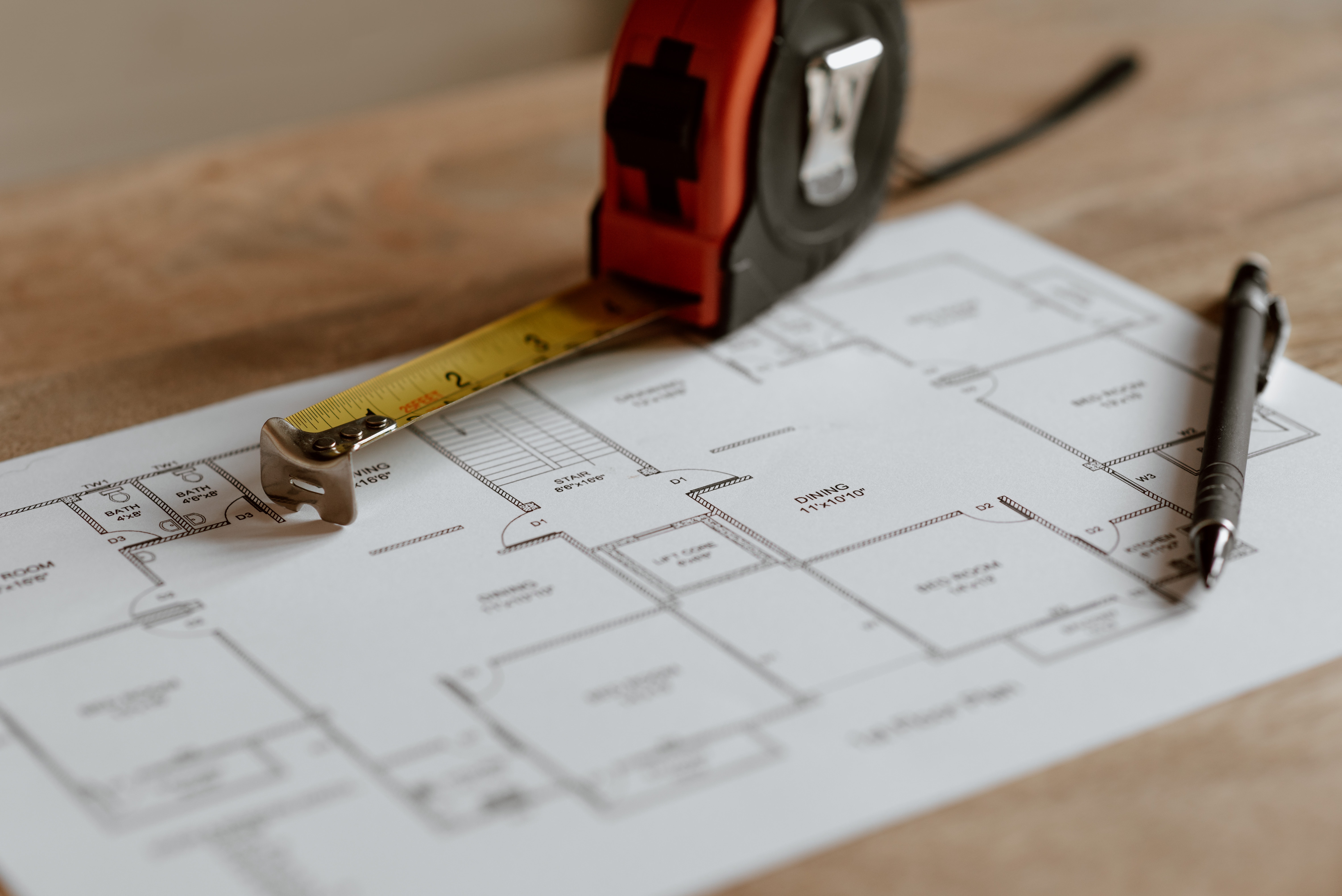
Introduction
There is a very famous quote by Lord Kelvin, "If you cannot measure it, you cannot improve it." Time, cost, and quality are the key players in managing a project. Time and cost are quantitative, whereas quality is often referred to as a non-measurable parameter. This might not hold entirely true. Read through this to find out how to measure quality in construction projects.
What gets measured gets managed. Quality is a subjective matter, but fundamentally it means customer satisfaction, matching the standards, and fit for use.
One of the ways to improve quality or demonstrate the efficiency of good quality in the project is to measure it. It sounds simple, but unlike time or cost, there is no single measure of quality in construction projects to compare it with another.
Takeaways
In this contemporary world where design and construction requirements are growing complex, managing quality becomes vital to handle modern-day building challenges. Using the correct tools and digital solutions for measuring the quality of construction, the construction industry will bring advancement and better work culture to produce a more efficient process of building contemporary facilities on time, within budget, and with the best quality.
Having reiterated the importance of quality in a construction project, measuring and quantifying quality become important. These new and advanced techniques must be applied to measure the quality and are promoted to get good results in improved quality standards in construction projects.
4. 3 High Level Quality Management Approaches In Construction Industry
Introduction
Quality is a habit. A habit which has to percolate down to the last part of the hierarchy in any organisation or ongoing project in order for it to be consistent. Some of the most acknowledged and prevalent methodologies adopted by industry leaders and top quality experts are :
- Kaizen Approach
- Six Sigma theory
- PDCA approach
Takeaways
It’s the right time to adopt a digital solution for the quality management of your construction project. We are here to help you develop this digital quality strategy and keep you updated as per the changing and continuously evolving construction industry.
5. Kaizen Approach for Improving Construction Quality process
Introduction
Today we're going to take Kaizen Approach up close. But first, let us find out where this methodology developed. The definition of kaizen comes from two Japanese words: 'kai' meaning 'change' and 'Zen' meaning 'good' which combined gives the term "continuous improvement" This concept was first introduced in the 1980s by the Japanese car company Toyota.
Kaizen method believes in achieving quality improvement by developing habits of making small but significant changes.
The construction industry has three major aspects: Capital, Time, and Quality, and Kaizen Approach focus on these three aspects. Earlier construction organizations planned two elements for customer satisfaction. For example, if the client demanded the completion of a project on time with high quality, the expense was greater. This ideology changed as people expected good quality & timely delivery of projects on a budget. This led to the development of different methods of achieving customer satisfaction. Prime principles of the Kaizen Approach are explained here with leading examples.
Takeaways
The Kaizen method is a high-quality management approach applied widely in the construction industry. This can only be achieved if the entire workforce has a positive attitude towards the approach and maintain enthusiasm throughout the life cycle. New organizations might find adopting the kaizen approach easier than existing organizations with old management systems. This might take time to reach every department of the organization and reflect beneficial results. Kaizen uses a cost reduction procedure that helps achieve quality within a budget.
6. Lean Approach for Improving Construction Process
Introduction
As we discussed earlier, the lean approach is widely adopted in the construction industry. The reason behind this is simple, basic steps with high yielding results. But what is the lean system? What are the principles of the lean approach? How does it benefit the construction industry?
All your questions will be answered in this story but first, let us understand how the lean approach was developed!
Lean methodology is one of the techniques which focuses on customer satisfaction through quality. It was first introduced by Toyota Motors in the 1920s but was not widely applied till World War-2. The international group of Lean Construction first coined this approach in 1993. It was initially adopted for the manufacturing process in a controlled environment, but later, it was successfully adopted in a wide range of industries through some lean modification approaches.
The lean approach is a holistic quality management approach that uses a wide variety of tools. Lean construction divides the whole process into two main aspects: Planning and Control. It uses its six principles to achieve continuous improvement, providing efficiency and reducing wastage.
Takeaways
Hence, one can say no system is without defects, but with a proper management system and giving it the correct amount of time, the issues can be resolved. The lean approach is widely adopted as a quality management system due to its benefits and because this model gives highly efficient results. Although developed for a controlled environment, the lean methodology can be adopted for wide-scale use such as construction and provide high customer satisfaction.
As we are about to conclude these approaches with one last remaining PDCA cycle, we will move forward to how to make a quality control checklist. This, combined with a centralized quality control system, a digital tool such as digiQC, and the adoption of high-quality control approach, will recognize the organization as high quality producing firm. This, in return, will benefit society and help in providing high-quality service to clients within budget.
7. PDCA Cycle for Improvement of Construction Quality Process
Introduction
Doesn’t perfect quality requires a lot of effort from the management team? It requires timely management of multiple resources that are transmitted via a large number of people in the same or different organizations. This generates demand for upholding the new market trends that ease these processes and aid in achieving predetermined goals to fulfill clients’ expectations. Now let us first understand how the PDCA cycle was developed and what are the multiple resources used to support this cycle.
PDCA Cycle was first developed by a management consultant Dr. William Edward Demings in the 1950’s. It is also popularly known as Deming’s cycle. This model helps in building a continuous loop for controlling & improving processes. It is a very basic model which makes it more accessible in the Indian construction industry that is in the revolutionary phase of project management systems.
This approach divides the processes into simple basic steps. It helps in improving processes in-country and eliminating repeating errors. This is a stand-alone method but is also adopted in lean methodology as a valued tool.
Takeaways
There are always negative and positive sides to a thing. But there is always scope for improvement for reducing disadvantages. PDCA cycle can be adapted for a wide range of construction organizations i.e from small-scale companies to large-scale organizations. PDCA Cycle has a very basic model which makes it easily accessible. Thus, one can Adopt the PDCA cycle for a wide variety of applications in the construction industry and can ensure quality control is enhanced.
Here we conclude cases of high-quality management approaches used by construction industry individuals. We discussed four high-quality management approaches and detailed the principles involving each approach. Any of these approaches can be adopted by construction industry individuals to provide superior quality for customer satisfaction.
8. Six Sigma Approach for Improving Construction Quality Process
Introduction
In our last story, I discussed the principles of the kaizen approach and how it is applied in the construction industry. Now let's discuss the six sigma principles.
The six Sigma approach is a high-quality management approach first used by car production company Motorola. The Greek letter 'Sigma' means deviation. In mathematics, 'Sigma' is used for the term of standard deviation from its mean. Hence six-sigma means six factors contributing to deviation resulting in defects. Six sigma helps in making a product with zero defects.
Six sigma is an analytical and data-driven process that uses a wide range of tools to achieve improvement. This approach aims at reducing variation in processes, in turn providing consistent and desired outcomes. It is a top-down and resource-intensive approach. It focuses on process improvement by controlling the 6 M's of the production process. It has integrated DMAIC Model for continuous improvement. Six-sigma is a highly effective method designed for achieving customer satisfaction.
Takeaways
The conclusion stands that the only way to implement this complex methodology is by adopting a holistic approach. This method is very efficient and preferred over another method as it considers six factors of deviation. This is a salient feature of this method and adds value to this method. The six-sigma approach is the top to the down approach, which is a standard approach used by construction firms worldwide.
Along with this, there are certain things that we need to keep in mind when we are developing quality control methods. It includes crucial steps such as developing standards checklists, doing root cause analysis, and keeping up with emerging construction trends in the construction industry.
9. Introduction to Four Continuous Improvement Methodology in Construction
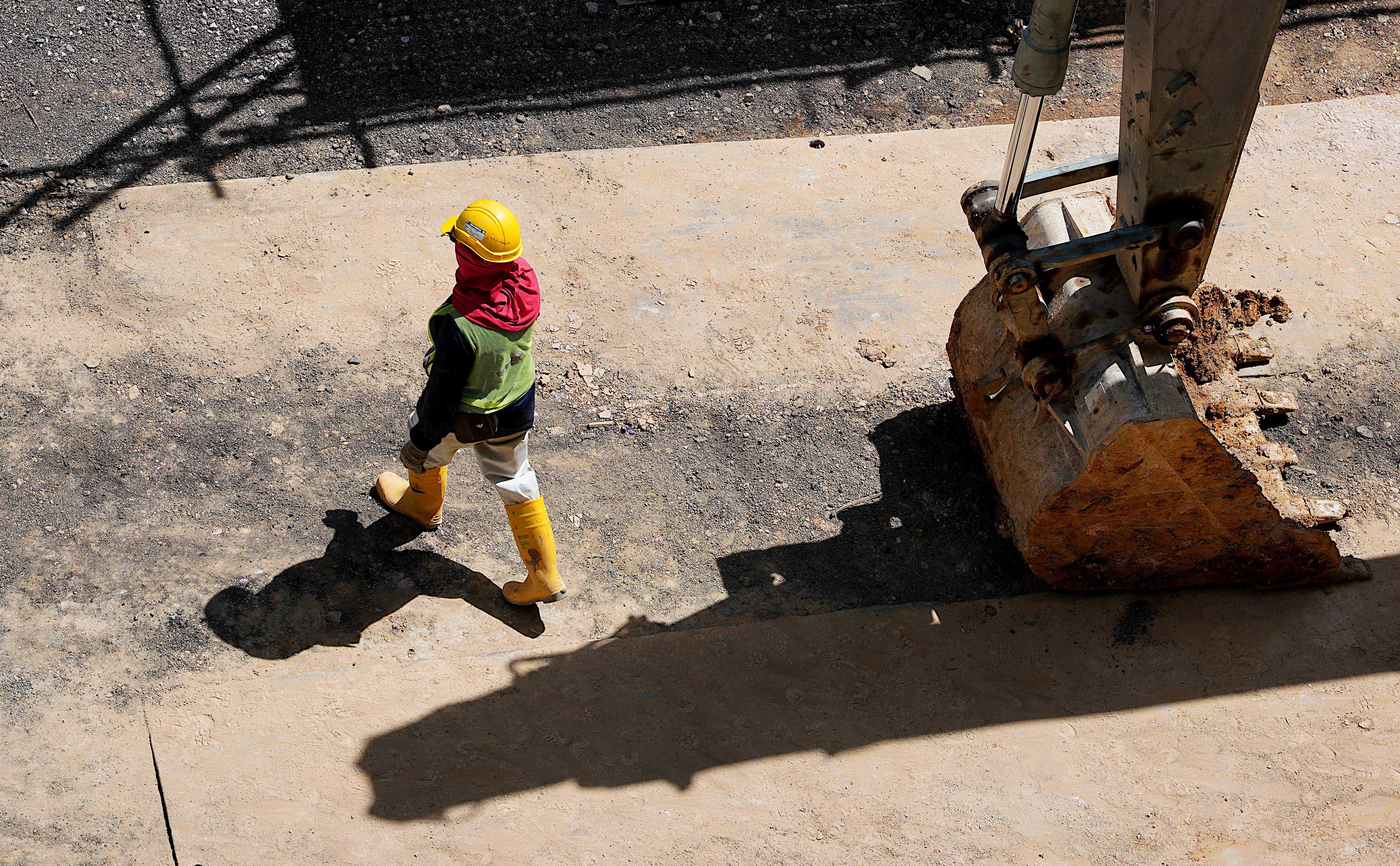
Introduction
In the construction industry, everything comes with a manual. We have standard operating procedures for different construction activities, and we need to follow them to produce the correct item. But where are standard operating procedures for quality practices? There are many approaches listed in multiple books, but which are the ones we should adopt?
This question poses such importance as it will later define the organization's very fabric. The construction industry is adapting to significant changes by focusing on proactive problem-solving approaches. These approaches may vary, but the focus is to eliminate or reduce the imminent threat of quality loss.
These approaches tend to eliminate or reduce risk probability at its root-cause level. Even if the problem occurs, the solution can be provided easily using them. Meanwhile, using these approaches helps us utilize the opportunity to understand the root cause of the risk & adapt the system to avoid future confrontation with it. This leads to continual improvement in the system through real-time data-driven techniques.
These approaches were first adopted in the industry in a controlled environment. Adopting them in the construction industry has a different interpretation as it has a vast number of techniques & environment is not controlled. Here I have listed four approaches and how they can be applied to the construction industry.
Takeaways
As we understand these approaches, we also need to understand each of them personally modified with changes required for the construction industry. In the following stories, I will explain each of these approaches in detail with examples prevalent in the construction industry and how they reduce the amount of wastage & rework. These approaches also adopt a centralized quality control system in order for more effective quality control. The centralized quality control system, along with the PDCA cycle, is adopted by digiQC to provide the highest level of the quality control system.
10. How to do Root-Cause Analysis for Quality Data
Introduction
Unpredicted problems occur in construction every step of the way. But these are generally fixed with temporary fixed which is similar to treating symptoms, not the disease. Instead, root cause helps you in identifying the problem from where it originated and contributing factors that lead to the occurring problem.
But first, we need to understand what root cause analysis is, what are the requirements to conduct root cause analysis and how it should be conducted? The following blog sheds some light on these issues.
Takeaways
Thus, the article sheds some light on how root cause analysis should be done and how beneficial it is to provide quality construction to clients with keeping budget in mind. Making root cause analysis a widely used construction technique will help in reducing non-conformity costs. Along with this, it can help in saving material and time which will in turn boost the economy for the construction sector.
Before understanding the importance of root cause analysis, one must understand that there is a dual approval procedure Maker-Checker that digiQC follows. It helps in enforcing strong values of accountability, transparency, and continuous improvement in standard operating procedures.
11. How to create Quality Control Checklist
Introduction
In the construction industry, quality control is required to ensure the predetermined standards are being met during the execution phase. Although, standards set during the start of a project contain many specifications for a single item and need to be checked at a different stage of execution. This is where the quality control checklist comes into the picture.
QC checklist is a very important part of quality control and affects various aspects of construction projects. For starters, the document helps in establishing accountability and transparency. At another point in time, it can help in root cause analysis for finding a solution to a problem. But all this is only possible if the proper checklist is prepared for which analysis is to be done. The checklist also helps to minimize the quality-related risks on the site if made properly. So, it becomes very important to prepare a checklist that does reduce the risk but can help in identifying the root cause in case of any issues on site.
Takeaways
Quality is the uttermost priority in the construction industry. Construction material, goods, and services being costly, proper quality control may help in reducing rework and maintenance costs. This will help to deliver a project on time and within budget.
This can be achieved if a quality control checklist is properly created and implemented on the project. This will not only help improve the quality of the current project but also help process improvement and decision-making for a future project through the data available through quality checklists.
With digiQC, you can create a standardized and customized quality control checklist to fit the requirement of the project. To understand this, use the templates provided by digiQC. These templates are of great help as they cover key points to be considered while constructing a specific project.
You can also refer to the case studies and get an insight into how digiQC helped stakeholders to increase efficiency and provide early delivery of a project. These are backed by facts, statistics, and data taken from real sites where digiQC was implemented.
12. Centralized System for Quality Control Process
Introduction
There is always a hierarchy or methodology followed to complete a certain task. When we define a system for controlling a process, we essentially create standard guidelines to follow or certain steps to endure that the execution has taken place to produce a quality product.
Since the tagline of digiQC is “focus on quality,” it certainly has adopted a methodology for quality control. First, we will discuss why quality is important.
Delivering quality is important for customer satisfaction and maintaining a reputation. The effectiveness of quality control depends on various factors such as quality process, actual quality control, and its analysis. Quality control processes and strategies are established to identify any deviation in quality as per specification, and improvements are made based on the available history quality data.
Since quality is of utmost essential and is the very fabric of the organization, we must first understand the types of quality control systems prevalent in the construction industry.
Takeaways
The centralized system is a very effective method with the very least drawbacks. This drawback can be resolved and can make the centralized system faultless. But when a centralized system is combined with digital tools like digiQC, a centralized system becomes more efficient and reliable. Thus, one must consider taking aid of such technologies to improve their quality process and can increase their goodwill in the market.
Since we discussed the quality control system, we should also understand that this system, along with digiQC, also helps in finding the root cause of these systems. Root cause analysis is certainly a tool that can be used to mitigate risk and avoid the same kinds of problems in a repetitive manner. Thus implementing a quality control system with digitized tools such as digiQC can help us achieve supreme quality, prestige and customer satisfaction.
13. 10 Tips for Quality Control in Construction Project
Introduction
Quality in the construction industry is an integral factor in growing a business, maintaining a reputation, and generating profits.
But not everyone can control the quality of their projects. Research shows that over half (54 percent) of construction defects "can be attributed to human factors like unskilled workers or insufficient supervision," and 12 percent are based on material and system failures.
Takeaways
Construction quality management is as simple as the above-discussed points. The method might not be elaborate but must be efficient enough to avoid quality-related problems and reduce the quantity of repair and rework on the construction projects. Some people use continuous improvement methodology for a robust quality management plan. Any one of these tips can bring significant improvements to the quality of the project, but abiding by all of them can get tremendous results in the company's favor.
digiQC is undoubtedly the best solution for all of your quality management-related issues. From documentation to checklists to inspections, everything is handled through it.
14. How to Write a Construction Quality Control Plan?
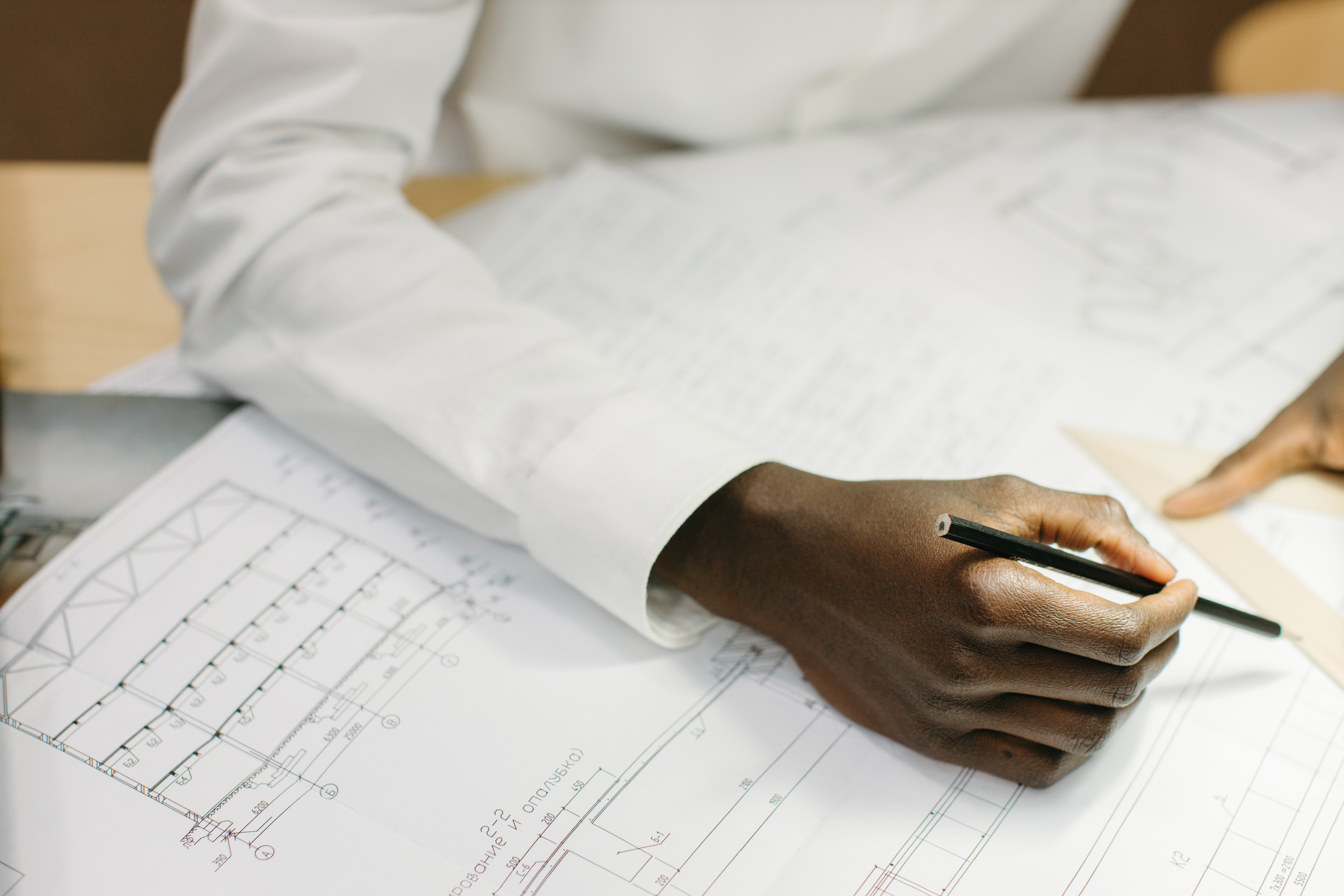
Introduction
Failing to plan is planning to fail. In construction, it is essential to plan every step to follow the planned schedule and avoid overruns. Quality is the main parameter of the project management triangle, and hence planning to control quality is a must for project success.
Planning without action is futile, but action without planning is fatal. Follow this through till the end to be equipped with the basics of making an effective quality control plan.
Takeaways
Building a construction quality control plan is essential in delivering products or services that meet customer expectations. And planning this quality control is even more critical to the project's success and building a solid reputation in the construction industry because quality always sets one apart. Quality control checklist are an essential criteria for making a quality management strategy. Always remember that quality is the best business plan.
To summarize the essence of the quality control plan in a single quote is to believe that, "An hour of planning can save you ten hours of re-making." Make time for a good strategy because half the war is won in the general's tent.
15. Maker-Checker-Approver-Auditor Quality Control Process
Introduction
Quality in construction is crucial and is given the most importance in accessing the value of the property built. But maintaining quality is also a sophisticated process. When one talks about quality control a central quality control seems to be an effective way.
But in the central quality control system, the most important bit of the puzzle is the hierarchal system of data transfer and dual approval requirement in order to ensure quality. But how is it done? What are the roles and responsibilities? Let’s discuss this in detail and get a better understanding of it.
Takeaways
Having an extra set of experienced eyes overlooking the eye reduces the chances of a small mistake turning into a big accident. But this also makes clients aware that the data provided to them is double-checked and they need not worry about construction quality. This also brings transparency to the system and inter-relations between the agency providing the facility and the client.
Now when we talk about this dual approval, we need to talk about how digiQC enforces the dual approval. But for this first, we need to understand how to make a quality control checklist. These checklists as we discussed earlier are frameworks to assess quality when audits take place. digiQC offers quality control solutions for Project owners, contractors and consultants with the smart features and high-end digital systems.
16. Best Quality Management Practices in Construction Industry
Introduction
The internationally well-accepted institution for project management, PMI, has defined Quality as “the degree to which a set of inherent characteristics fulfill requirements” in its Project Management Body of Knowledge (PMBOK). Quality management is a subset of project management that focuses on customer satisfaction and defects prevention.
‘Anticipate the difficult by managing the easy’ is the line said by Lao Tsu. To manage efficiently, adopting efficient and best practices is essential for project success. Hereafter discussed are the practice overview, requirements, and best practices involved in quality management of a construction project.
Takeaways
Compromising quality practices can never lead to more profits and long-time success. It is not a trade of profit versus practices. The construction companies that model the best practices and upstanding principles end up as profitable companies because adopting the best approach is not what you do once you are good, but it’s what makes you suitable.
DigiQC can help you digitalize the best practices to achieve the desired quality standards and make your job of managing Quality less cumbersome.
17. A guide to improving and elevating your third-party inspections for quality
Introduction
Let us develop a situation here. Where you pose as a construction developer and I am a contractor you hired to execute the construction project work. I say in my inspection report that all quality standards are upheld and all regulations are followed. But doesn't the question arises that I am in control of the inspection report and I can alter it to my convenience?
Generally, that doesn't happen in the construction industry but what if there are some mistakes I am unknowingly making? Who will point it out? Here come third-party inspection services providing agencies to save the day.
Third-party inspection agencies are unbiased observers who whatsoever have no stake in the project. They provide both developer and contractor with facts backed by IS Standards and inspection methods. They understand the client's requirement and aid the contractor in correcting their course of action to comply with the standards of the building code.
Takeaways
From the above facts, one can conclude that having digital third-party quality inspections will help you elevate construction quality as well as attract customers as you're being quality conscious as well as an environmentally conscious company.
With this, it's safe to say that an investment in third-party inspection agencies is good and will save you a lot of money in the long run.
With the digiQC instructions app, you can also eliminate communication errors and standardize visible and transparent communication for more accountability and authenticity.
18. Why Inspection and Test Plans (ITPs) are critical for your construction business
Introduction
Being in the competitive field of construction demands a lot of efficiency in today’s date, given the swift progress across different parts of the field. The growing scale of the projects is also increasing the pressure on a project’s efficiency in terms of all parameters of construction:
- Time allocated for the project
- Cost of the project
- Quality output of the project
Among these, the project quality becomes a major concern since both time and cost factors are dependent on it. The assurance of this quality falls under the responsibility of a quality engineer who performs the quality checks based on an important document called an Inspection Test Plan (ITP).
Inspection Test Plans are:
- Plans for the work order/program of quality inspections
- Statistical test procedures with reliable results
- Multi-step processes with test points and verification protocols
These ITPs are crucial to a quality assurance program—and hence, are carried out before, during and after the project realization process. But do you know why it is so important?
Takeaways
Due to the complexity and ambiguity of manual Inspection Test Plans, modern construction businesses have started using digital tools that simplify the entire process. Given the multiple teams in a construction projects, especially in the large-scale metropolitan projects, the digital platforms are preferred the most due to:
- Easy customisation according to the team’s expertise and project requirements
- Quickly shareable reports with comments and action points for different teams
- Instant verification by multiple professionals in both on-site and off-site teams through mobile channels
- Better end-to-end quality management with overall analytics and other useful features
19. 10 Factors that Affect Construction Quality Management
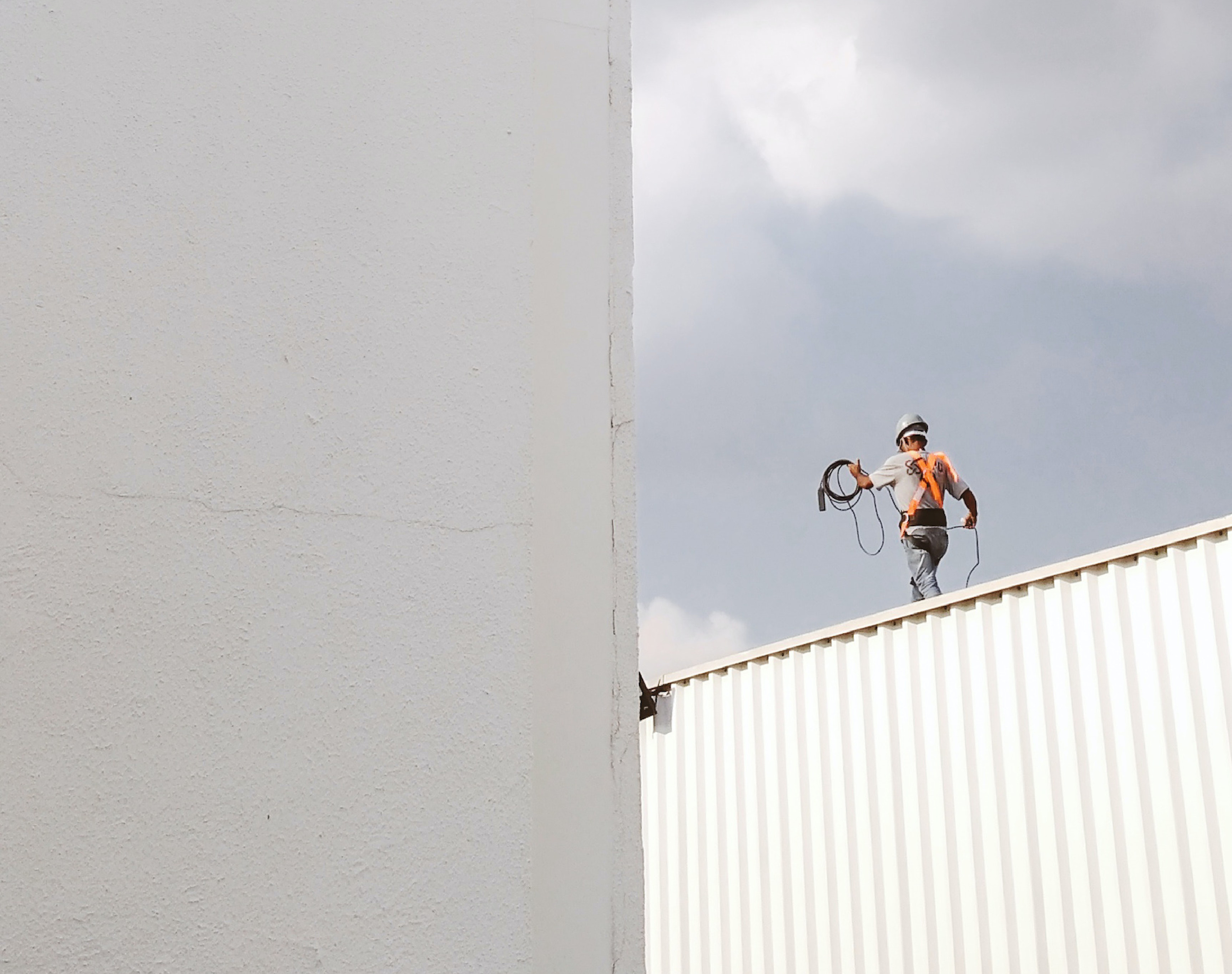
Introduction
Quality is not by chance; it is always an outcome of the intention of sincere effort in an intelligent direction. It begins with the intent, which is fixed by management.
Managing quality includes making wise choices of many alternatives. There is no point in making sound and logical decisions or actions without maintaining the standard.
The success or failure of a plan involves many factors. Without proper planning, leadership, and management, no quality system can function correctly.
Certain factors affect the quality of a construction site which has to be handled accurately. All such aspects will be discussed hereafter.
Takeaways
To summarize, handling all such factors wisely will ensure the expected quality of a construction project. All these factors can be tackled digitally by DigiQC, which will make your work simple and easy. In the era of digital evolution, upgrade yourself and your project to DigiQC and optimize the quality of your construction project. Always remember, Quality is the best business mantra.
Can’t find the information you are looking for? Get in touch with our team of quality management experts who can take you on the right direction for your project!
If you are simply looking for a quality solution that makes the best use of the above mentioned methods and techniques, try digiQC that helps you customise quality checklists in a hassle-free online software.
Learn more about the features here.