Isn’t quality the ultimate measure of performance? Indeed, it is! The quality of the product gives us an impression of how indulgent was the service provider towards the assigned task.
In this blog, I indulged myself with two prevalent quality control methods, to see the positives, negatives, and grey areas in these methods adopted widely throughout the construction industry.
I used the following criteria to evaluate the methods:
- Value
- Decision-making
- Data retrievability
- Authenticity
- Rectification procedures
- Risk mitigation timelapse
- Non-conformance cost
- Usage ease
There are many more parameters that are identified that are used here for evaluation. But first, let’s understand what is quality control and how it is part of a bigger system of quality management.
What is Quality Control?
Quality control is the oriented process of management to achieve outlined expectations. Quality control is about delivering promised quality on time with established standards, verified through the standard testing procedures.
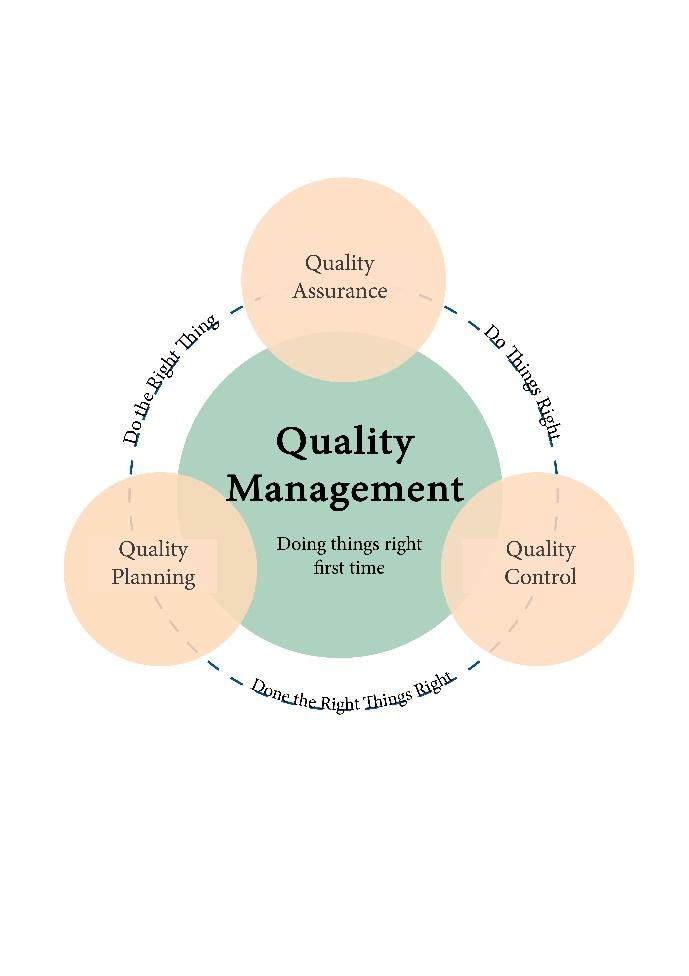
First, let me shed some light on how quality control is being carried out using a conventional method.
Conventional Quality Control:
When a construction contract is awarded, management & inspection systems are set up & are placed in the system to ensure the quality is in accordance with the requirement of the project owner.
These frameworks help the stakeholders to monitor the activities & identify problems along with planning solutions to a given problem. Checklists and inspections are done by on-site engineers and experts to make sure that the quality of the project is as per the standard required.
Conventional systems used paper-based systems & experts visit site for overall quality control. In this system, after work is executed on site, the quality checks are done & are subsequently assessed by experts. The main drawback here is it takes a long time to be reviewed by an expert.
If a QC fails & the management is notified, the construction phase has effectively progressed to the following stage. This results in wastage of resources & costs the management their valuable time & money.
One of the many problems encountered during this process is altering of reports & lack of accountability. These are huge problems & affect the unwavering quality of the organization. As the checklists and other resources to be filled for quality control are paper-based, they can be modified effectively by anyone at any level.
This generally drives the absence of responsibility when the administration is attempting to find the responsible party. It costs a huge amount of time to identify the party in question while the project has come to an abrupt stop.
Paper-based checklists get fixed & obsolete. These checklists are common for a specific item & cannot be changed as per different requirements. This tends to be a problem in a project with various kinds of predetermined things. Additionally, keeping up records for similar work process are not associated. Different stages of activities are reviewed by isolated individuals, the paper-based trail is hard to connect. The capacity of reports likewise is an issue as they are liable to be lost, stolen, damaged, or misplaced.
All the on-site activities are carried out with aid of construction drawings. These drawings are subject to alteration due to changes in architectural & structural designs. Drawings can be mishandled & activity is potentially completed using the old design. This results in severe quality control failure along with the disrupted timeline. Also, an audit requires in-person review which reduces the frequency.
These factors raise some serious questions about using the conventional way of quality control for project owners. Even though the project is well-planned, failure in quality control leads to reconstruction & financial instability.
The quality control using such an outdated method is high risk due to communication gaps, language barriers & misplacement of important documents. Though the solution lies in front of us in form of digital technology. Advancements in artificial intelligence can be used for the development of quality control tools.
But what is the solution for such a stated problem? As witnessed by the construction industry, the aftermath of such problems is catastrophic. Let me give you an example.
Earlier in construction, we used mild steel reinforcement for countering the tensile stress on structures. The flaw if the system was exposed during the catastrophic earthquake of Gujarat in 2001. In the aftermath, structural engineers come together to find out the solution for these. They increased the grip of reinforcement steel by providing ribs and grooves. Today we see HYSD bars are the most prevalent choice for RCC Construction
Although quality control is one of the important criteria, it is yet to be benefitted from digital evolution. Quality control is still carried out using a conventional method which has numerous flaws in its design. Innovations & new businesses are using this opportunity for their potential benefit & are bringing digital evolution to the construction industry.
Quality Control through digiQC
Individuals have adopted digital technology in many forms. Automation & digital tools are being used from the beginning of the project to the very end. As we know quality control is an important aspect of the development process, and there is a need for digital tools in this field.
digiQC is such a tool developed by Spaceify Technologies PVT LTD. DigiQC is cloud-based software that inspects on-site work in real-time. It is available for both iOS & Android users.
digiQC has two platforms namely a web module & mobile app. The web module is for set-up, monitoring & analysis to be used by project managers & executives for audits, quality checks & rectifying any problems occurring in the workforce. While on the other hand mobile app is used by projector engineers & supervisors for onsite quality control.
digiQC helps at different stages of Quality Management. During the planning stages, it provides project owners & management personnel to establish the timeline & set up a checklist along with guidelines & criteria for certain activities. During quality assurance, it helps set up guidelines for a specific item that is to be produced along with the production time & quality to be achieved.
Quality Control is the stronghold of digiQC. It helps solve all the problems that are faced by project owners while using traditional quality control. It has cloud-based storage which is accessible through a mobile app only by authorized personnel. It provides tamperproof real-time inspections & photos.
Customized checklists are available & step-wise inspection reports remain together. It has the feature of uploading drawings wherever required in the checklist. Also, audits can be made remotely & more frequently. This adds to the advantage that whenever QC fails, management facilities & project owners are notified instantly. It also helps in the identification of responsible parties & the actions to be taken for rectification of the flaw.
digiQC provides optimal solutions through real-time data collection & analysis. It makes data remotely accessible to every person in the commend chain & reduces the possibility of rework & wastage. digiQC is one-step solution to better quality control & regulation on site.
Conclusion:
In conclusion, all I have to say is that evolution has always benefitted human kind. We need to change our methods for the betterment of society and need to adopt these evolutionary methods as we have earlier.
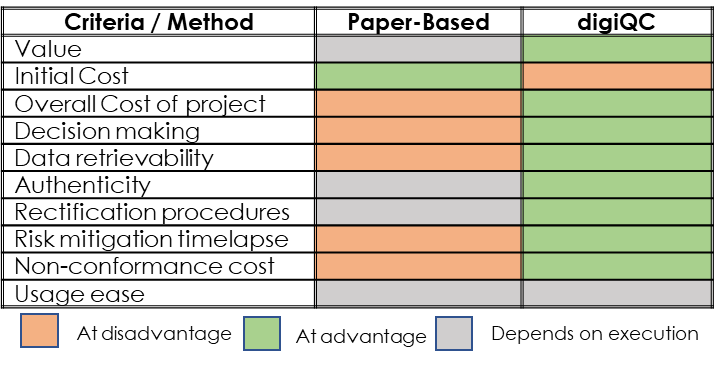
Conclusion
The stated facts give proof that digital tools such as digiQC has a great benefit over conventional systems. High-quality output through these is setting higher expectations among clients & workforce. As people are becoming more aware they are now preferring higher standards of quality management to reduce rework & loss. Training requirements to use digital technologies are also given attention. This upgradation of the construction industry from using a paper-based system to digital tools is long overdue. It will lead to digitalization of the development sector along with enhanced construction quality & time management.
Ready to adopt this effective quality control method? Give a quick read to the blog: Digitization in construction—An Overview and understand how you can take part in the digital revolution in this field.